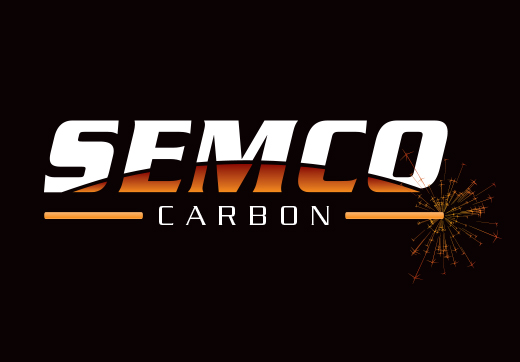
Five Keys to Success When Machining Graphite
Your Graphite Mill / Graphite Machining Guide
Graphite machining can be challenging, especially if you are not prepared to work with the combination of unique and messy properties of graphite. As a custom graphite machining facility as well as a supplier of graphite material blanks, we have answered may customer questions over the years about the difficulty of machining graphite correctly and the many unique design needs our customers have encountered. The following is a list of five key concepts to keep in mind when attempting to successfully machine graphite.
No Liquids or Coolants!
First, machining of synthetic graphite should be done dry without the use of liquid coolants. The use of coolants when working with graphite will produce an abrasive slurry when the coolant combines with the fine bits of graphite chips and dust.
The coolant fluid will also permeate the graphite materials through the open porosity of the material. Essentially the graphite will act as a sponge, as capillary action draws the coolant into the open pores. This contamination will cause problems when the graphite is used in an application that requires the inert nature of the graphite material.
Start with Dry Material
Second, the starting graphite raw materials you intend to machine should be dry before graphite machining begins. If your raw material stock has been stored outside or been exposed to water it should be baked to drive out any excessive moisture from the graphite before graphite machining begins. The combination of water and dust will make an abrasive slurry, which will dramatically reduce your tool life. This issue can be most clearly observed when cutting wet graphite on a band-saw.The dust does not exit the graphite material during cut and packs up in the kerf. Essentially the cutting tool re-cuts the same graphite chips over and over again.
Quality Ventilation System
Thirdly, it is very important to have an adequate ventilation system to contain and vent the graphite dust and chips produced during the machining operations. Graphite dust is electrically conductive and will find its way into every crack or opening in a machine enclosure. Static electricity will draw the dust to circuit boards and create short circuits when the build up bridges contacts.
Attempting graphite machining on a CNC machine that has not been specifically modified to handle the graphite dust is not an optimum solution and can lead to expensive damage and potentially void a warranty.
Sharp Tooling
Fourth, graphite machining should be done with very sharp tooling, adding a level of precision that helps to to prevent particle pull-out or edge chipping. Once certain components of cutting tools have lost their sharp edge they will fracture the graphite material or cause a blowout of an edge when exiting a cut during graphite machining. This is because the dull tool is pushing and not cutting the graphite material. Graphite has great compressive strength, but will fracture if the force is directed out of the material rather than into it. A tool made from micro-grain carbide designed for cast iron works well in graphite. Vapor deposition diamond coated endmills also work well as machining tools, with quality parts and components delivering high accuracy and precision, but can be very expensive.
"Climb Milling"
Fifth, it is a good practice when utilizing a graphite mill to ''Climb Mill'' or work from the outside into the graphite material. When milling pockets avoid leaving islands when the endmill cuts from the pocket perimeter into the center of a pocket. The island material will break out when the final island is removed resulting in a pockmarked cavity during processing. It is a better practice to drill a center hole and mill the pocket from inside to the outer edge of the graphite to mill it properly.