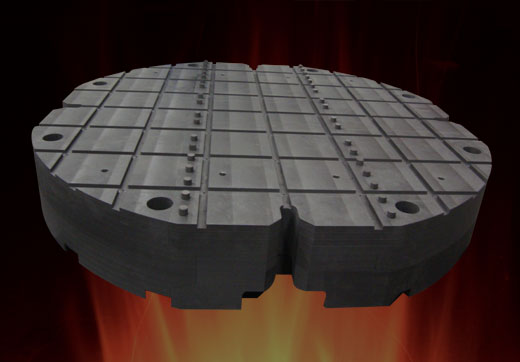
Challenges Producing a Large Diameter Graphite Disc
In machine shops, the size of the equipment limits the size of the pieces that can be produced. Occasionally, however, a client needs something bigger than a shop is used to handling. They need a graphite plate that’s 82” in diameter, for instance. Most shops, Semco included, rarely if ever work with a block of graphite large enough to cut this disk from.
Semco, however, is not in the business of turning down business or turning away customers who need graphite components. We’ve made our reputation as leaders in the field of graphite machining on handling just this kind of request, one that other graphite shops would turn down. While the size of this graphite plate was a difficulty for us in filling this order, it was not a deal breaker. Rather, it spurred us on to do what we do best: problem solve and innovate.
Block of Graphite
To solve a difficult problem, you must first recognize the problem for what it is. No graphite manufacturer in the world works with an 84” x 84” block of graphite, which would be necessary to cut an 82” inch plate from. Finding such a piece of raw material and machining it was therefore out of the question. Realizing this helped us see what we had to do: we would have to assemble the graphite plate from smaller pieces. These smaller sections of material would need to be machined individually in such a way that they could be assembled together. While this seems like an elegant (an obvious) solution, assembling a large graphite plate has its dangers. Assembled components are not much different than the human body -- they weaken and break down at the joints first. Whatever joining material we used would need to create a virtually indestructible bond to attain uniform strength through the entire component. Otherwise, the durability of the component would not be sufficient for the role it would serve for our client. So, finding a way to join the pieces effectively was a must. Semco has used graphite cement in the past, and we turned to this helpful material again for this job. Graphite cement has the virtue of creating joints that are actually stronger than the rest of the material itself. Once the cement is used to glue the pieces together, the entire component can be cured and the cement at that point is 100% graphite. There is no weakness at the joints.
Graphite Plate
After completing the machining of the smaller pieces, fitting them together with graphite cement, and curing the component, the job still wasn’t complete. Some further machining to the graphite plate still had to be accomplished. While the colossal size (by graphite shop standards) of the final piece was imposing, it did not faze the Haas GR-712, one of our most heavy-duty CNC tools in the shop. In fact, we were able to use the Haas to machine the component with a half inch per side to spare.
Some of the real secrets of our trade (ones we won’t discuss here) were how we moved and turned this piece (to machine both sides), then loaded, transported, and unloaded it. All these challenges were successfully navigated by our crew. Through this entire process, our very experienced employees had to find ways to bring to fruition this very complex job, which no one had done before. Semco’s reputation as leaders in graphite manufacturing derives from projects like this one, projects where the collective experience and brilliance of our engineers and crew are brought together to solve complex problems and innovate. We know how to get from a block of graphite (or several) to the component you need. And if we don’t, we’ll figure it out.