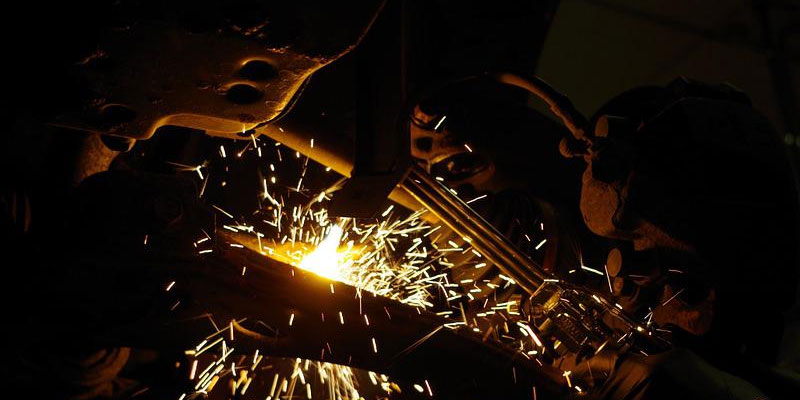
Debriefing Graphite Company Business
When a job for a set of graphite plates, or any other graphite components, comes into our office, many parts of this graphite company are set in motion. At Semco, little is wasted (our scrap rate is at an all-time low), especially not time. So when the office receives a request for a job, our staff communicates the specs of the job to the machinists. Our warehouse delivers the graphite plates or blocks to the shop floor. The cuts are then made by our skilled machinists, the components are tested and inspected, and the delivery department gets the components out to our customers on time. Whether we’re working with a repeat customer on graphite mold casting or with a new customer on battery components, we are thorough and communicate well with the customer throughout this process. The results of our system are customers happy with their graphite mold casting, battery components, or any other graphite component they have ordered.
In truth, most jobs that come to a graphite company like ours are not always as simple or straightforward as described above. Customers interested in graphite mold casting, for instance, are very concerned about tight tolerances and durability for their molds. Other customers aren’t sure what grade of graphite plates will be appropriate for their particular job. At Semco, we know that operating on auto-pilot will not deliver the results our customers expect. Many considerations come into our work, many decisions must be made, and much information must be communicated between departments, and between our office and the customer. To continue our work of reflecting and communicating better and more often, Semco has started a new program focused on debriefing jobs to find what has gone well and identify places for improvement. While we have always reflected on our work of machining graphite plates and blocks at Semco, we have discovered a way to systematize that reflection so that it is more inclusive and effective.
Debriefing Improves Jobs Like Graphite Mold Casting
The purpose of our new debriefing protocol is simple: highlight wins and call attention to opportunities for improvement. In these post-run debriefs, we especially aim to streamline our routing and estimation process for new and existing parts, and improve communication between departments and between departments and management. Twice a month we select jobs to discuss. For instance, we may have a job that requires us to cast several graphite molds for a customer. The scope of the debrief is limited. We make sure to create small, focused groups of personnel, specifically in this case the personnel involved in the graphite mold casting. When any group of people gather to learn from successes and mistakes, the most difficult thing is to ensure that everyone can speak candidly and freely. Many things can go wrong in complicated manufacturing processes like graphite mold casting or machining graphite plates into components with tight tolerances. Semco employees are encouraged to have open conversations in these debriefs about what worked well and what could be improved.
Graphite Company Policy: Always Strive to Improve
We do not choose the jobs to debrief randomly. Instead, we start with one job that had great results. Our Project Manager issues job briefs to everyone that will be participating in that debrief so they can be reviewed and fresh on everyone’s mind for optimum engagement. The conversations with the personnel involved with this job often yield useful information. We then look at implementing the lessons learned from that successful job in other current or future jobs. We also debrief a job where there were inconsistencies with the plan. Perhaps times were off, or routing was not accurate, or too little raw material was available on hand to run a routine job. The analysis in these debriefing sessions reveals the weaknesses in these jobs. The team then discusses a correction plan which it then writes up and implements for that job. The last steps are to identify the positive lessons learned from this process and make a plan to implement these lessons throughout all our applicable projects.
Good Communication Turns Graphite Plates into Components
This debriefing protocol is primarily looking at improving communication between departments, and between departments and the management team. Communication issues turn out to be where most problems with a job arise. The improved communication resulting from these debriefs translate into lessons that can be implemented throughout the jobs run on the floor. After running several debriefs, we have especially improved efficiency and accuracy of routing and estimation. Our Production Manager also notes that losses caused by estimation, improper machine selection, improper training of personnel, programming issues, and lack of customer documentation have all been raised and addressed by dedicated Semco employees engaged in open, honest, and safe discussions with their trusted colleagues.
Problems only get bigger if ignored. The priority we put on candid and frequent communication at Semco separates us from the competition and keeps our customer base loyal and happy.