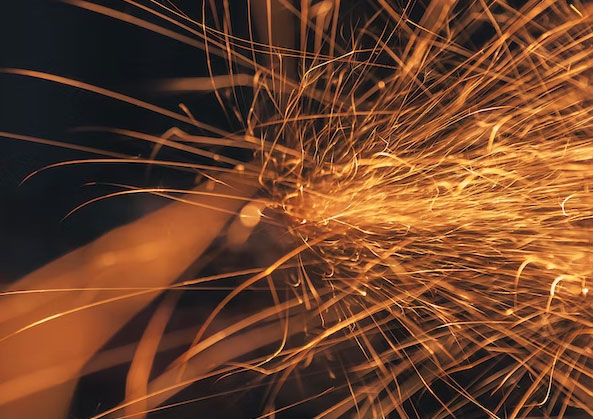
Designer Extruded and Isostatic Graphite
Graphite is Lubricating, and…
Graphite naturally has a unique set of physical properties that allows it to be used in environments where other materials would degrade or perform poorly. For instance, graphite can be used in conditions where traditional lubricants and other self-lubricating materials will fail. It can withstand high temperatures, corrosive media, and dry atmospheres, all while maintaining a low coefficient of friction and remaining dimensionally and thermally stable. But graphite as a lubricating material is typically not the first use of this wonder material that comes to mind. Most people, if thinking of graphite in an industrial setting, might imagine a graphite mold or a large crucible. The graphite used in industry is more often than not synthetic graphite like isostatic graphite, and is created by industrial processes that we will describe below. Think of synthetic graphite as designer graphite. It's like the naturally occurring stuff — it’s lubricating, it can withstand high temperatures, etc — but can be tweaked in the manufacturing process to have qualities that go beyond its natural qualities.
Not Your Grandmother’s Graphite Mold…
…Or perhaps we should say, not your great-great-grandmother’s graphite mold, since synthetic graphite was first created in the late 19th century. When produced of synthetic material, graphite components like graphite molds are made from two raw ingredients, powders and binders. Powders may include natural or synthetic graphite, carbon black, calcined petroleum coke, or other forms of carbon that are either byproducts of the refining industry or are mined.
Binders are the “glue” that holds the powders together. These binders, which are often coal tar or petroleum pitch, uniformly coat the carbon powders as they are mixed together. The resulting mix is then milled down to specified particle size. Once the ingredients are mixed and milled to a specific particle size, they are then pressed to become a solid component. There are two main methods by which this is done, each of which results in different final material properties.
Isostatic Graphite
Iso Molding
Isomolded carbon graphite is isostatically pressed, meaning a constant pressure is applied to all sides of the material as it is being manufactured. This results in a fine-grained material. This method, which produces isostatic graphite, is normally used for some of the finest grain carbon grades, often used as electrode material for EDM (electrical discharge machining). In fact, isostatic graphite is the preferred electrode material for 90% of all sinker EDM applications.
Extruded Graphite
Extrusion
In this method, the mixed powder is pushed through a die, resulting in a relatively softer part with a coarse grain size. As a result, extruded carbon grades are typically used in lower duty applications.
Baking
At this point in the process, the green material begins to resemble a solid material block, but it does not yet have the strength of the finished material. You cannot yet make a graphite mold out of this material. The binder has not been hardened yet and is just acting as a relatively weak adhesive holding the powders together. The green material must be sent through a controlled, oxygen-free baking process to carbonize the pitch binder and turn it into a very strong amorphous carbon. This process takes place in ovens, where the atmosphere and temperatures are closely monitored to ensure proper baking parameters.
Since the extruded or isostatic graphite needs to spend a certain amount of time in each temperature zone, it takes up to several weeks for a part to enter the oven and come out as machinable carbon graphite. During the baking process, outgassing occurs, meaning hydrocarbons in the pitch are driven off, leaving behind an amorphous carbon structure. The gasses push their way out of the material, leaving behind interconnected porosity. Graphite is thus an inherently porous material because of this outgassing. Carbon graphite manufacturers are able to take advantage of this network of porosity by impregnating it with various substances. This is what we mean by “designer graphite.”
Types of Graphite Impregnations
Oxidation Reduction Impregnation (NOX)
This impregnation is useful in preventing the oxidation of the binder pitch that holds synthetic graphite together. This impregnation coats the exposed graphite on the exterior of the component and also infiltrates the interior to coat any open porosity and reduce the effect of oxygen on the graphite component. While useful in several graphite applications, NOX is not necessary in a controlled atmosphere furnace or a vacuum environment. Additionally, 900℉ is the maximum temperature at which this treatment will provide a benefit of extended component life. Care needs to be taken so that the intended application process will not cause adverse effects to graphite impregnated in this way.
Phenolic Resin Impregnation
This impregnation is commonly used in the production of graphite heat exchangers, as it provides completely closed porosity and will withstand a wide range of temperatures and will work with a large range of chemicals.
Polyester Resin Impregnation
This impregnation is useful in closing any open porosity inherent in graphitic components. Common uses of this treatment include graphite displacers, steam seals, and pump vanes. The resin actually fills any open porosity exposed during the machining process. Once the bake cycle is complete, the component should be 99.9% solid and be able to perform as a seal. An additional benefit of the resin impregnation is an increase in strength and hardness of the graphite component.
Oil Impregnation
This impregnation is typically used in bearing and bushing applications where additional lubrication may be necessary. This kind of impregnated graphite is typically used in lower temperature applications.
Silicon Carbide Conversion
This process is actually a conversion of the outer layer of the graphite component into silicon carbide. The conversion process requires that a specific grade of graphite be used, as the graphite structure and its coefficient of thermal expansion are of utmost importance. If non-suitable graphite is used for conversion and the CTEs are incompatible, then the component is prone to fracture, spall, or crack on its initial high temperature run. Typical uses of this process include susceptors for semiconductor applications, optical applications, such as a mirror substrate for laser and radar systems, and industrial applications that may require an extremely hard heat resistant surface.
Babbitt Impregnation
Babbitt is a very popular and inexpensive self-lubricating bearing impregnation, typically used for dry applications at room temperature up to 350℉. Additionally, this impregnation can be used for submerged applications due to its high corrosive resistance and long wear life. The impregnation consists of approximately 90% tin, with the balance being copper and antimony. This impregnation can be used for items such as pump and meter bearings, seal rings, thrust washers and any number of roll bearing applications.
Purification
This process involves taking graphite material to extremely high temperatures and purging the hot graphite with chlorine gas to drive out any impurities. This process will usually produce extremely clean graphite with less than 5 ppm of residual ash content. Purification is valuable in the semiconductor, nuclear, and quartz manufacturing industries.
Spray Metalizing
The process of spray metalizing consists of surface coating graphite components with a layer of metal. Metals such as zinc, copper, aluminum, cobalt, nickel, and bronze can be applied through spray metalizing. This process is useful in electrical contact applications.