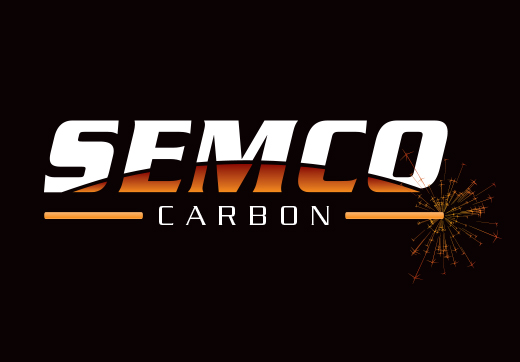
Explaining The Coefficient of Thermal Expansion in Graphite Materials
At Semco Carbon, we are constantly thinking of new, relevant and useful topics to incorporate into our periodic blogs.
Let's Discuss The Coefficient of Thermal Expansion
In a recent meeting our application engineers were working on a specific issue to assist one of our customers. A customer of ours had been experiencing premature component breakage in a new high temperature process they were testing. Looking at the specifics of their application, we determined that this experience would provide a good example of the importance of the Coefficient of Thermal Expansion.
We thought this specific case study and other relevant experiences could be used to shed light on the importance and proper evaluation of the attributes found on a typical graphite material specification sheet. Over the next few months we will be posting a series of blogs detailing each attribute listed on the standard material specification sheet.
What is The Coefficient of Thermal Expansion
For this particular blog, we will discuss the Coefficient of Thermal Expansion. By definition, Thermal Expansion is the tendency of matter (in our case graphite), to change in volume in response to change in temperature, trough heat transfer. The Coefficient of Thermal Expansion is the value that allows us to calculate the amount of volume change that will occur, with the change in temperature over a specific range.
Why is This Important?
Why is the Coefficient of Thermal Expansion important in our industry? Graphite is definitely susceptible to physical changes, due to the extreme temperatures found in many of the typical applications. That being said, one graphite grade will perform differently than another under the same variations in temperature. Understanding this attribute, and being able to anticipate how a specific graphite grade will perform under field or process conditions is important. It allows the ability to customize solutions based on customer's set parameters.
Going back to the meeting that produced the initial idea for this blog, I will detail the problem one of our customers was confronted with, explain our thinking process, and present the solution we offered, as means of explaining the before-mentioned attribute.
Our customer was in the process of setting up a new line of furnaces, designed to run at higher temperatures than their regular furnaces. For the new graphite components, the customer specified the graphite grade which had been used successfully in their regular furnace line for many years. Yet, during test runs of the new furnace, on multiple occasions, either the graphite components or the connecting parts, manufactured by our customer from various other materials, would fail, exhibiting cracks.
Our analysis focused on the higher temperature, since none of the components experienced the same degree of failure in our customer’s past applications. The graphite materials utilized in this new furnace were capable of withstanding the operating temperature and process environment. Since the parts that experienced failures were interconnected, we assumed that the issue had to be related to how various materials work together within the system. A quick glance at the materials specification sheets, revealed vastly different coefficients of thermal expansion, between the graphite and other materials used. We came to the conclusion that the difference in coefficients, caused materials to expand in volume at different rates. That in turn caused significant stress on all connected parts that resulted in the premature failures. One question remaining was, why the same materials, did not exhibit the same failures in the customer’s standard furnace line? The answer was both operating temperature and the ramp rate or speed at which those temperatures were reached. . While stress was experienced within the components in the standard line of furnaces, it was not enough to damage components. Raising the upper operating temperature to a new threshold level was causing excessive stress between parts.
Most graphite material specification sheets will list the value for the Coefficient of Thermal Expansion, but the value is set over a known temperature range or just extrapolated based upon limited data. It is vitally important to understand that all graphite manufacturers do not use the same range of temperatures to set their published Coefficient of Thermal Expansion values. Most of the commercially available graphite materials will have different values over different temperature ranges. As an example, the Coefficient of Thermal Expansion from 100-500 degrees is different than the Coefficient of Thermal Expansion over 3,100 to 3,500 degrees.
After the analysis of data was complete, we recommended a different graphite grade. One with a lower Coefficient of Thermal Expansion value, as well as suggested that our customer change various other non-graphite materials within the system. Successive tests, done after the implementation of the new materials were successful, showing little or no damage to the internal components, which had been experiencing the premature wear.
This case study revealed how changes perceived as relatively minor, could in fact change dramatically the operability of heat treat systems. It also revealed that materials considered proven and reliable, could in fact fail, if not integrated correctly.