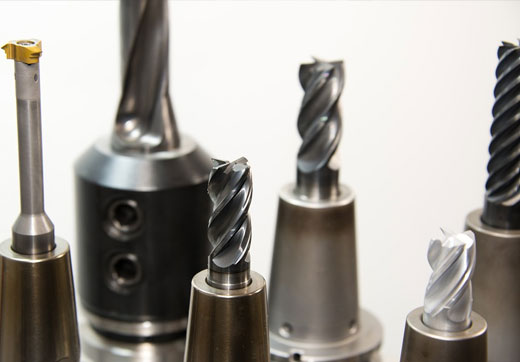
From Graphite Blocks to Graphite Component
We’ve covered many details in this blog about our machining of graphite components, including the different types of graphite that we use, design considerations, and some case studies about how we solved particular problems that our clients have run into. In this blog, we would like to provide a grand overview of the process that a block of graphite goes through in our facility to become finished graphite components ready to ship to our customers. More specifically, we want to tell you about the machines that do the cutting, shaping, and finishing of graphite blocks until they become the parts our customers have ordered. Let’s begin the journey.
The first step in the journey is, of course, the arrival of raw material. Raw graphite blocks arrive at our facility and are then stored in our climate-controlled indoor warehouse, where they are protected from the elements. These large rectangular or round blocks of graphite are more often than not first worked upon in the saw department. There, the material gets cut into particular sizes based on the specifications for each job. We rely on a variety of large saws capable of cutting pieces up to 100”+ plus in length and over 68’’ in height. On our shop floor we also have a number of smaller saws that provide us with the capabilities to cut virtually any size parts from virtually any size blocks.
From the saw department, the cut shapes are distributed to one of our 3 main value-added departments: the mills department, the lathes department, and the grinding department. Complementing these departments are smaller ones that provide us with sanding and diamond cutting capabilities.
The milling department consists of multiple CNC mills. Various sizes and capabilities allow us to make parts as small as a few grams, and as large as 144’’ long x 84’’ wide. The height capability on some of our machines reaches 60’’. We rarely receive requests to machine graphite components of sizes that challenge our capabilities. When that rare instance occurs, we work with the customer to discover a solution.
Our lathes department has a large vertical turning center, and a variety of traditional CNC lathes. Here, product can be turned up to 17’’ diameter x 40’’ long. Again, these dimensions are almost always sufficient for any request that we receive.
The grinding department specializes in parts that require special finishes. Our grinders allow us to machine product to finishes as smooth as is required of particular graphite component designs.
Throughout the whole process, our CAD (computer-aided design) department is responsible for providing our team with the custom programs to machine complex shapes. The programmers and engineers in this department work closely with our clients to ensure that every detail of the needed graphite component is accounted for in our machining plan. Our QC (quality control) department is also there to make sure that the parts are machined to conform to their plan at all stages of production.
After QC gives the go-ahead, the finished product travels back to the shipping department where the parts are boxed or crated and then secured in order to arrive in perfect condition to our customers.
All in all, 30 or more people, and a multitude of technologically advanced machines, are involved in this process of creating custom graphite components from the raw blocks of graphite sitting in our warehouse.