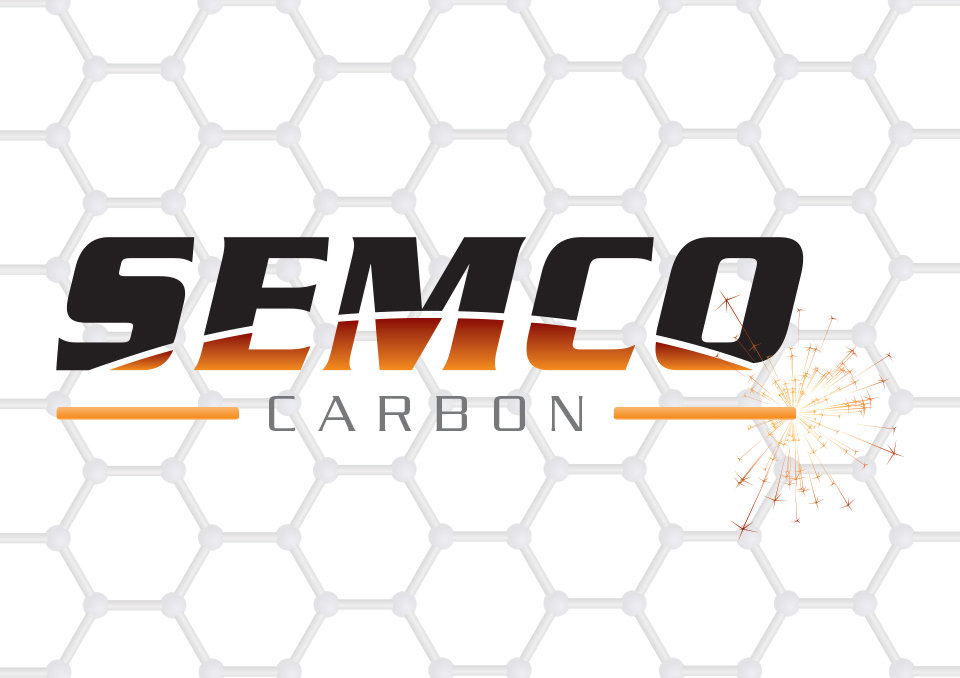
Graphite and Oxidation
A recurring issue we hear about from people using graphite components is graphite oxidation. This term describes unwanted redox reactions where oxidizing agents modify graphite properties negatively. Hence, especially at high temperatures, steps need to be taken to eliminate oxygen presence so that oxidation and deterioration of graphite components is avoided. Semco strives to educate our clients who order custom graphite components about the proper environments in which those components should operate. However, new clients will come to us expressing their frustration that graphite components are failing long before they should. One reason to work with the synthetic graphite experts at Semco is that our graphite specialists know all the ins and outs of graphite, its many strengths and its fickleness in certain situations, like when it is exposed to oxidizing agents at high temperatures. We’ll share a bit of our knowledge here about preventing graphite oxidation for anyone using graphite components in their manufacturing processes.
Isn’t Graphite Resistant to Chemical Reaction?
Despite being known for its stability and resistance to many chemical reactions, graphite can oxidize under certain conditions, especially at very high temperatures. Graphite oxidation refers to the redox reaction between graphite and oxygen, leading to the formation of carbon dioxide (CO2) or carbon monoxide (CO). The process of graphite oxidation generally occurs in the presence of oxygen at temperatures above 400-500°C (752-932°F). However, the exact temperature at which significant oxidation occurs can vary based on factors such as the specific type of graphite, its purity, the presence of impurities, and the environment.
In addition to elevated temperatures, which facilitate the reaction between graphite and oxygen, graphite oxidation can occur more readily in the following conditions:
Presence of Oxygen
In environments with high oxygen concentration, redox reactions are more likely to occur. However, sometimes oxygen is required, even at high levels, in certain manufacturing processes. For instance, in an earlier blog we told the story of a client coming to us with a very specific problem related to oxidation. This particular client was using an intricate graphite fixture in a process designed to produce solar panels. The process operates at very high temperature (over 2500 deg. celsius) in a controlled atmosphere that is purged with argon.
The client wanted to introduce oxygen into the system to cool the system rapidly in order to repair a component, then restart the system as soon as possible. The client had some knowledge of graphite oxidation, but had no hard data. For this particular application, the graphite grade used is a high-purity ISO-molded grade, a very dense, very strong graphite grade. The client believed that such a grade would not oxidize. However, while the client was partially right -- high purity, dense graphite degrades more slowly -- but we helped the client design a cooling system that would only inject oxygen below 425℃, the point at which graphite begins to oxidize. This saved the client’s specialized graphite component from degradation while only minimally affecting the cooling process.
Presence of Surface Defects
Impurities or defects on the surface of the graphite can accelerate oxidation. Luckily, Semco can work with clients to choose the best graphite grade for their particular application, a grade that is less likely to become damaged under specific conditions. The hardness or softness of graphite material is dependent on the grade of synthetic graphite, as well as whether the graphite has been impregnated with another material. Our graphite experts use their extensive knowledge of synthetic graphite grades and types to pinpoint just the right material for our clients.
Conclusions
This process of graphite oxidation is a concern in various industries where graphite is used in high-temperature applications, such as in furnaces, reactors, or other industrial processes. To mitigate oxidation, protective coatings or treatments may be applied to the graphite surface to prevent direct exposure to oxygen or high-temperature conditions. Additionally, using high-quality graphite with fewer impurities and maintaining controlled environments can help minimize oxidation. You can rely on the graphite experts at Semco to guide you through the steps you need to take to protect your valuable graphite components from degradation due to oxidation.