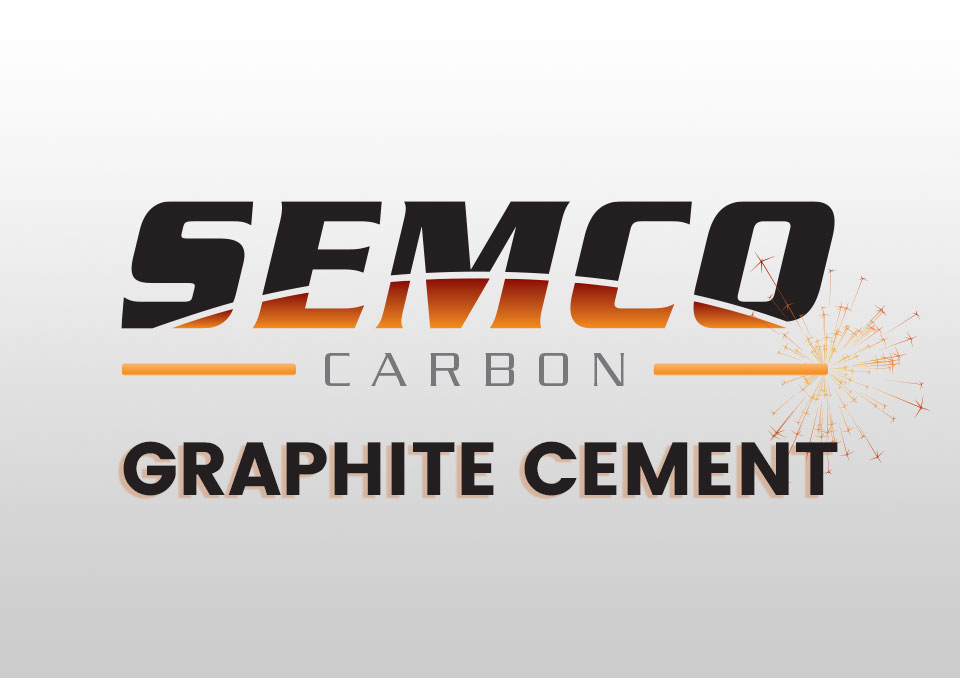
Graphite Cement
It’s a Hollywood trope: the camera takes us inside a smelting factory or other metallurgical hothouse to establish an atmosphere of intense industrial heat and violence. In the center of these images is usually some sort of giant crucible bubbling over with what looks to be flaming magma. Think the orcs’ sword factory in the second Lord of the Rings movie. As huge as these factories appear, one imagines the even bigger factory that would be needed to produce that giant crucible!
Sure, it’s the movies, but there is a real-world answer to that mystery of the giant crucible: graphite cement. In our industry, graphite cement is a wonder material, allowing machinists to manufacture graphite material into components that would be difficult to impossible to create otherwise. Occasionally at Semco, a client asks us to produce a part that is either too big to produce in one piece based on our machines’ capabilities or on the size of the raw graphite blocks available. Sometimes the geometry of the graphite component simply won’t allow it to be machined in one piece. In these instances, Semco relies on graphite cement. A material in the form of a paste, graphite cement is applied to joints and creates a bond that is 100% graphite once cured. As any carpenter knows, the joints of a structure are the places most vulnerable to breaking and failure. With graphite cenement, however, the strength of the joint it creates is on par with the rest of the material. It even remains secure at temperatures to 5400ºF (3000ºC) in inert or reducing atmospheres.
Graphite cement can be used for many different purposes. In some cases, individual pieces are machined, then joined with graphite cement to form a strong assembly. In other cases, graphite cement is used to join graphite blanks that can then be machined to the finish geometry. There are the cracked parts, dies, and fixtures that graphite cement can be used to repair. And the list of uses goes on: graphite cement may be used to cement insulation in place, affix sight tubes and pouring spouts, join rams and punches, set molds and dies, seal plugs, repair subsectors, join carbon foam and felt, and fix broken resistance heating elements. In all these cases, the process for application to graphite materials or graphite blocks is simple: the paste is applied to cleaned, prepared surfaces and cured at 275ºF for five hours.The joint will be 99%+ pure graphite. At that point the product can be brought to any operating temperature. If absolute purity is desired, the material can be brought to a temperature past 1300ºF, at which point the material is free of any residual organic contaminants. In most cases, when graphite cement is properly applied and cured, the joints it forms are stronger than the substrate.
If you are curious about the possibilities offered by graphite cement, Semco engineers and machinists are happy to advise on the use of this wonder product. On our shop floor, we use the product on a regular basis, and we always ensure it is available for our customers.