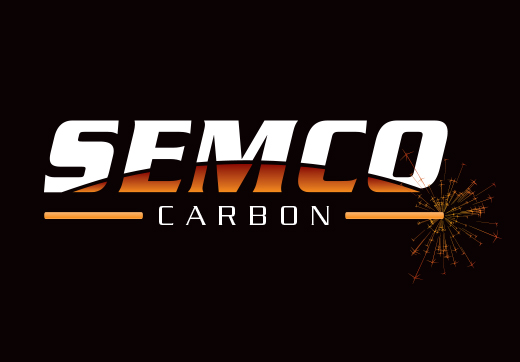
Graphite Compressive Strength vs. Graphite Flexural Strength
Flexural Strength with most graphite material is on average only 50% to 60% of its Compressive Strength.
By definition, Compressive Strength is the capacity of a material to withstand loads tending to reduce its size. Measured, it is the value obtained by plotting applied force against deformation. At compressive strength limit, the material will fracture, or deform irreversibly.
Flexural Strength is defined as the ability to resist deformation under load. It is measured with the help of The Transverse Bending Test. In this test, a sample is bent until it fractures, using a 3 point flex test technique. Flexural Strength is measured at the highest stress experienced within the material at the moment of rupture. These specifications apply to graphite materials and are commonly found on material specification sheets.
Confusion can occur, if the definitions are not correctly read, interpreted or understood. Both parameters refer to the ability of a material, to resist deformation (withstand loads). The difference between the two parameters is due to the methodology applied to calculate the loads. Compressive Strength is measured when force is generally applied uniformly on one surface, while the opposite face is fully supported.
Flexural Strength is measured as a bend test. The material is supported on 2 points placed at the edges of the material, while force is applied in the center of it. Intuitively, the Compressive Strength of a material will be greater than the Flexural Strength of the same material.
We had an experience that demonstrated how the wrong interpretation of these materials specifications resulted in component failure. We received a customer call concerning an application using graphite plates in a sintering process. The customer informed us that some of the graphite plates had fractured during use. We have produced the plates working closely with the customer, based on their process requirements. Additionally, these plates have been used for years by the customer with no failures.
Their system consisted of one graphite plate used as a base, fully supported by the bottom of the furnace, a stack of parts to be sintered, and finally a top graphite plate. The graphite plates, allowed for a threaded metal rod secured to the bottom of the furnace, to penetrate the center the assembly. A large round nut was used to secure everything in place, and apply the necessary pressure. This design resulted in an assembly that was subjected to mainly compressive forces throughout. The graphite grade was more than capable to withstand the compressive forces applied within the system as originally designed.
When attempting to resolve the fracturing issue with the customer, we looked into any possible changes within the process. We discovered that the originally designed part, which was virtually a solid disk, has been re-designed by the customer for weight savings, into a ring, with a large I.D. Our team realized that the top lid was no longer supported. Once force was applied to the center of the lid, the material fractured.
In this instance, the lid was no longer experiencing compressive strengths, but in fact it was experiencing flexural strengths. This resulted in reducing the maximum force the lid could withstand by approximately 50%. With this design change, the original material was no longer suitable in this application. The solution was relatively simple. Higher strength graphite material was used to replace the original graphite grade.
In conclusion, while the process did not chance, the different geometry of the parts caused a switch from compressive force, to flexural force. The updated lids with adequate flexural strength were tested, and ran flawlessly. The lids are currently in full production and performing as expected.