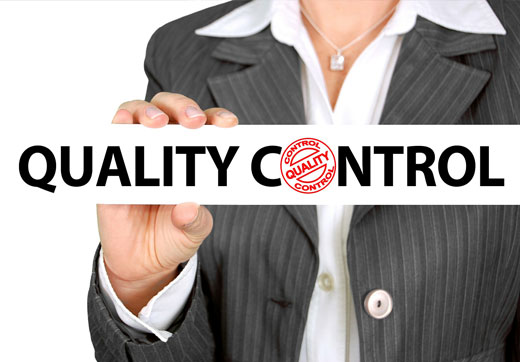
Graphite Coring
When a client orders a machined graphite component from Semco, we do everything possible to give them the best deal we can. Providing value to our clients on graphite product dovetails perfectly with other values we hold, such as eliminating waste and promoting efficiency. Cutting corners, though, is something we do not do. If you order graphite product from Semco, it will be of the highest quality, machined to your rigorous specifications. Within this commitment to highest quality graphite components, there are still opportunities for savings for both the client and for Semco. These instances usually arise from smart engineering and our deep knowledge of the graphite material that we specialize in. In this blog, we will explain one such cost-saving (without any sacrifice to quality) technique we have developed at Semco: graphite coring. While drilling holes through the middle of graphite bars is not a new idea, we have worked to develop a way to avoid wasting the drilled graphite as spent dust. This process allows us to provide a better value to the customer by utilizing less material while producing additional graphite rounds to be used on other projects.
What we do is this: when machining certain graphite components, we use a special drilling technique to core out the block to produce a smaller graphite rod that can be used in other applications. Imagine a larger round with an I.D. (inner diameter) in it. For the lay readers, that just means there’s a hole through the middle of the round. This coring does not weaken the graphite round to the extent that it matters for the particular graphite component (if it did weaken the graphite product, we would not perform this operation on it). The traditional method of machining the I.D. would employ some sort of drilling, and the result would be a huge dusty mess. A boring bar with an insert attached to it would open the I.D. to the required diameter, and the result would be a perfectly fine part. However, much dust would be produced to machine the hole out. We consider this a waste of good material.
To minimize this waste, we have developed corring tooling that allows us to extract the core in a size and shape that will allow it to be reused in the machining of other graphite components. The coring tool looks something like a cylinder, with cutting inserts on one of the edges and a mounting tail to mount in a lathe chuck. This tool cuts a certain diameter groove inside the material, close to the I.D. size needed, while producing a core. Depending on the size of the graphite component, this core could be very small or big enough to be quite useful in the machining of other graphite product. No matter the size of the graphite component being machined, the smaller diameter that we can extract will have a purpose and does not turn into useless dust.
When we are able to save a round of material that has value associated with it, we certainly do ourselves a favor. But with this method, we can provide our customers with reduced raw material costs as well. We provide our clients with a percentage credit on raw material cost for the core we save. Also, saving smaller rounds simply keeps value in the raw material. These produced cores don’t just sit in some dusty corner or our warehouse, but are frequently used for other in-house projects. Developing this coring technique on our shop floor clearly made a win for the customer and a win for Semco.
This is just another instance of thinking out of the box or, should we say, out of the block, that we are known for here at Semco.