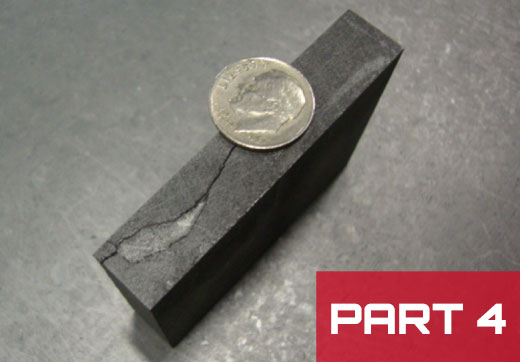
Graphite Material Quality Series - Blog 4: Cold Chunk
Series Introduction:
Semco has made its name in graphite manufacturing, an industry that requires great investment in tools, technology, and training. Our machining capabilities and ability to customize graphite elements for clients’ manufacturing systems make us a go-to for companies that require industrial components made of carbon. This series of blogs will focus on a more behind-the-scenes, but no less important, aspect of our business: the selection and utilization of high-quality graphite material. At Semco, we take choosing the right graphite grade for each project very seriously because we know that the finished component, no matter how skillfully tooled, will only be as effective and durable as the material with which it is made. Occasionally, a client will request that we use their graphite material. To these requests, we generally respond that we prefer to provide the graphite (although we do take jobs where the client insists we use their graphite). This series of blogs will explore what can go wrong with graphite material and why it is crucial to any project that raw material be examined and chosen by experts in the field of graphite manufacturing.
Cold Chunk:
“Cold chunk” is a term used to describe a particular result of a flaw in the graphite manufacturing process. Synthetic graphite is produced by mixing materials such as coke, pitch, and/or other binders. Large machines mix the materials to achieve consistency in the quality of the graphite. However, if these mixing machines are not properly cleaned between runs, or if foreign objects or substances make their way into the mix because of improper storage or handling of the material, cold chunk can result. In this condition, distinct masses appear in the otherwise uniformly mixed material. These masses can be problematic for several reasons. For one, they can contain contaminants. Graphite is one of the most inert industrial materials, and manufacturers count on this inert quality of the material. If a reactive substance enters the mix, this could cause problems downstream for companies using graphite components in an assembly that handles reactive material. Foreign masses may also detach completely from the graphite block. If the cold chunk is not discovered before the graphite is machined into components, those masses could detach while the graphite component is in use, causing serious problems to a manufacturing assembly. Cold chunk is not a condition anyone wants to encounter in their graphite material.
Cold chunk appears most commonly in lower graphite grades, such as electrode and extruded grades which are associated with larger particle sizes. Higher quality graphite grades such as ISO-molded grades, which are composed of smaller particles and have higher densities, are rarely found to contain foreign masses, although it occasionally happens. Typically, the manufacture of lower-grade graphite material has looser quality control processes, and is thus more susceptible to producing graphite material with cold chunk. No matter the graphite grade we are working with, Semco goes to great lengths to mitigate these defects by monitoring the material during the manufacturing process. Our engineers and machinists on the shop floor are highly skilled at recognizing material flaws like cold chunk. When flawed material is identified, we segregate the originating blocks or rods for further inspection, and we dispose of any material unfit for machining into the highest quality components.
As we have stated earlier in this blog series, we strongly recommend to clients that we machine parts in-house. However, we do occasionally sell raw material to clients who prefer to machine their own components. In these cases, if a flaw is spotted by the client in the material, we will of course replace the defective material. The reason we so strongly encourage our customers to allow us to produce finished product in-house is that we are confident in our ability to spot flawed material early in the manufacturing process. Often, our Quality Department will identify graphite blocks with cold chunk before it even makes it to the shop floor from storage. Spotting flawed material early saves on manufacturing costs by preventing wasted machining time and energy on unfit material. Our team detects and isolates any defective material before it has the chance to be machined into a defective component.
Our attention to detail and deep knowledge of the material we work with every day means that going with Semco with your graphite machining needs is always a good decision.