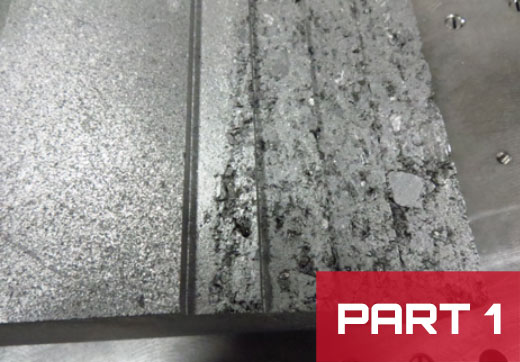
Graphite Material Quality Series: Part 1
Note: This blog is the first in a series. Other installments will run, one a month, for the next several months.
Semco has made its name in graphite manufacturing, an industry that requires great investment in tools, technology, and training. Our machining capabilities and ability to customize graphite components for clients makes us a go-to for companies that require industrial components made of carbon. This series of blogs will focus on a more behind-the-scenes, but no less important, aspect of our business: the selection and utilization of high-quality graphite material. At Semco, we take choosing the right graphite grade for each project very seriously because we know that the finished component, no matter how skillfully tooled, will only be as effective and durable as the material with which it is made. Occasionally, a client will request that we use their graphite material. To these requests, we generally respond that we prefer to provide the graphite (although we do take jobs where the client insists we use their graphite). This series of blogs will explore what can go wrong with graphite material and why it is crucial to any project that raw material be examined and chosen by experts in the field of graphite manufacturing.
The focus of this blog will be on blend contamination, a term that describes a flaw in graphite production during the mixing process. Graphite is made from either coal or petroleum coke which is crushed and screened to separate different size particles for different graphite grades. Once the particles are separated this way, they are mixed with binders such as pitch or resin, along with iron oxides. At this point, you have the basic blend for producing graphite. High quality graphite, whatever the grade, will be composed of uniformly-sized particles to ensure that the strength throughout the block of graphite is uniform. This uniformity is essential to producing reliable graphite components that operate consistently and predictably. To get back to the mixing process, though--when particles of different sizes find their way into the same block of graphite, blend contamination has occured. This situation can come about in several ways. Perhaps the most common cause of blend contamination is when a graphite manufacturing plant fails to clean its equipment between runs. Materials of a particular grade left in the mixing machine are then incorporated into the next batch of a different grade of graphite. Sometimes, to clean the machine, manufacturers will use the first few runs of a different graphite grade as a clean-up for the prior grade, extracting the prior material in this way. When this is done, the resulting blocks of graphite should be recycled internally by the manufacturer rather than sold as a particular graphite grade, but sometimes these blocks appear on the market.
Blend contamination can be spotted by careful visual observation. In a contaminated batch, one size grain material is concentrated in one area of the block or rod while a different grain size is concentrated in a different area. The material appears as if it is composed of two different blends, which in fact it is. While this contamination would seem to be easy to spot, there is one factor that makes detection less likely: the “bark” that all graphite material comes with. This outer layer, which is removed by most shops before machining, conceals the flaws in the material. A block of graphite can look perfect to the untrained eye, but when the bark is removed, or the block cut into, blend contamination can then become apparent. This difficulty gauging the quality of a block of graphite is why Semco encourages our customers to allow us to quote machining and materials, and not just toll processing machining. Our employees are trained to recognize blend contamination and we have a quarantine process when contaminated material is discovered. Thus, we can ensure that no components machined from contaminated graphite are delivered to a client.
As should be apparent, material quality is a top consideration in graphite manufacturing. Semco employees’ expertise in recognizing flawed graphite, as well as our company’s insistence on machining parts using only blocks of graphite with a consistent graphite grade, make us a reliable source for the highest quality graphite components. We will work with clients who want us to use their graphite. However, our experiences have taught us that in the long run, it is a better business decision for both Semco and our clients to allow our graphite experts to handle raw material acquisition for projects. Carefully selected graphite plus our cutting edge machining equals the highest quality graphite components. We know our clients expect no less.