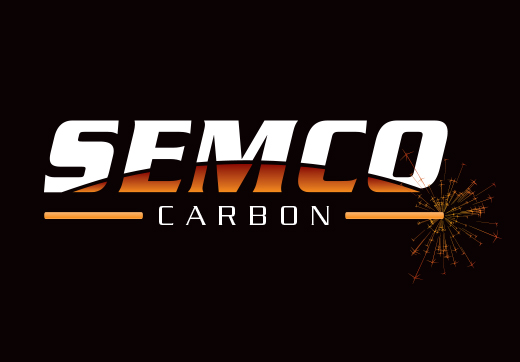
Graphite Casting Molds: Your Cost Saving Solution
All About Graphite Casting Molds
Graphite Mold Production
Graphite has been used in mold production for over 50 years by large and small businesses alike. Advancements in available materials have created the options that allowed graphite to be used in a variety of applications. Ingot graphite molds are commonly used in aluminum, and precious metals (such as gold and silver) casting. Benefits of graphite permanent molds are realized by combining the low cost associated with machining graphite and high strength common to graphite materials, providing an economical alternative to other molds in the zinc-aluminum metal casting industry.
Graphite Grade
Proper selection of the graphite grade is essential in the performance of the manufactured mold. Generally, given the relatively large porosity, extruded graphite grades are not recommended in the manufacturing of graphite molds requiring fine detail. There are certain high density extruded grades that could be a solution when budget restraints or low volumes dictate an economical solution. Most of the time, applications using fine detail graphite molds, utilize either molded or Isostatically pressed graphite grades. Both families of grades display high density and small particle size, perfectly suited for very high strength, very good finish and excellent life. Isostatically molded graphite has the best qualities for intricate mold designs and high volume runs even beyond just the high density.
Regardless of grade chosen, graphite is extremely stable and display high density in the most common grades. It will not warp, twist or check when molten metal is introduced. Parts can be cast with higher accuracy than sand or iron processes. Graphite can also be stored indefinitely without changing shape, rusting, oxidizing or deteriorating in any way.
Graphite Mold Application
Basic graphite ingot molds have a tapered edge design, for easy extraction of the ingot. The more intricate graphite ingot molds are produced per customer specifications, using production methods that incorporate CAD design as well as CNC machining. In general, graphite ingot mold applications represent a good alternative to metal molds, especially when the end user is looking for the quality, feel, strength and durability of a metal part but not necessarily the associated costs. That is why graphite molds have seen in recent years a sizable increase in demand.
Our exposure to customers experiences over the past 40 years, allows for drawing conclusions when it comes to proper use of graphite dies and offering appropriate materials. It is true that choosing the proper graphite grade and properly machining the correct configuration dictate how well the mold is going to perform. It is also essential that proper operating procedures need to be followed in order to achieve the desired results.
Graphite Properties
As an example, the failure to preheat the mold could result in damage of the interior surface and even cracking of the mold in extreme cases. The photo below exemplifies this condition. The end user rushed the process, the result was the damage of a complete set of molds. Graphite molds stored in wet areas or outside need to be thoroughly dried before contacting any form of molten metal. The water retained in the pores of the graphite will turn to steam when in contact with molten metal. This is a dangerous situation for the operator and detrimental to the mold.
Mold manufacturers need to provide customers with the best product for the application, but also serve another important function, educating clients on any potential pitfalls.
Dispelling Misconceptions
In the end, we are going to discuss various misconceptions regarding graphite. A common misconception that graphite is weak and can be easily damaged. Graphite is a crystalline structure. It is therefore very rigid and it retains its dimensions extremely well. Graphite is very strong and can withstand a significant amount of stress. When used in a process that is not designed correctly it can damage or even break, but from a production standpoint this is a preferable outcome to the warping of other mold materials in a tight tolerance situations. Materials which will deform can potentially produce entire runs of rejected parts, until the problem is discovered.
Additionally, the life expectancy of a graphite mold is commonly thought to be relatively short. That is totally a misconception. In metrics representing overall performance, high density graphite approaches the same performance as metal materials, and if we account for the reduced production costs of these high density graphite molds, the cost per run can be better in relationship with the cost of other materials.
Graphite Ingot Molds
In conclusion, graphite molds can and do represent a viable, cost efficient solution for both large and small businesses. The engineering, design and manufacturing process, coupled with following the proper operating procedures can result in parts that meet or exceed customers expectations in both performance and service time.