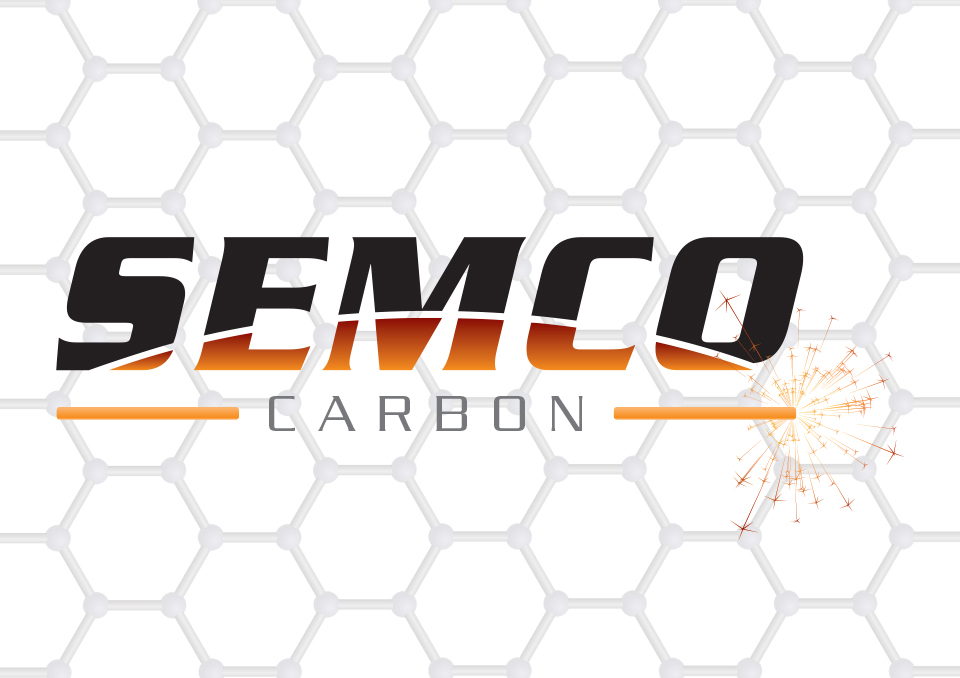
Graphite Property: Thermal Shock
In business, as in many other parts of life, there really is no replacement for experience. The schooling and enthusiasm of the apprentice is no match for the master’s depth of knowledge acquired from long experience. At Semco, not only do our graphite specialists have deep personal experience in the field, but our decades of custom machining graphite material have helped to build great institutional memory that gets passed down from long-time to new employees. We frequently use this blog to detail what we’ve learned from some of our experiences solving customer problems. Recently, we learned something about a particular property of graphite—thermal shock—from solving a problem for a customer in the precious metals refining industry.
For years we had been supplying this customer with various sizes of graphite ingot molds. We had an excellent understanding of their processes and their product line, so our graphite material was dialed-in to their process.
On our last visit, the customer wanted to discuss a new 1000oz. size graphite ingot mold. This mold would be used in a brand new flameless tunnel furnace, similar in construction with the other furnaces they were already operating, but larger in capacity and size.
Our discussion with their engineering team quickly settled on the idea that we would not change the graphite grade used on this line, since the process is basically the same, and the graphite grade used in all other processes worked so well.
Since the customer wanted to test this new line, we quickly produced prints, which were then approved by the customer. We then machined a batch of ten graphite ingot molds for the customer to test in the new furnace. Neither we nor the customer were prepared for what happened next./
On the first run, three of the graphite ingot molds fractured, and two more molds fractured in the second run. For reference, it is typical for these types of graphite ingot molds to run up to 100 cycles before they exhibit any type of erosion.
When graphite components don’t hold up well in a process, we usually consider the graphite grade first, since there is great variability in conditions that different material grades can handle. Since the same graphite grade was working fine in all the customer’s other processes, we decided that an investigation of their process, and not the graphite grade, was what was needed for this line.
To picture the set-up we’re discussing here, the reader should bear in mind that this is a large graphite ingot mold (1000oz. capacity) that is brought up to red hot temperatures in order to melt precious metals into the bar shape, then cooled so the bar can be extracted. As we inspected the new furnace and compared it with the other two they had in-house, we quickly recognized a big difference in how this furnace was operating vs. the others. The other furnaces had a cooling process that allowed the graphite ingot mold, and the precious metals inside, to cool slowly for approx. 20 minutes before being transferred onto a cooling plate for rapid cooling.
In the new furnace, the process was reversed. The rapid cooling happened at the beginning, followed by a slower cooling process afterwards. This reversal was a big deal. Placing a large graphite ingot mold at almost 2000℉ on a cooling plate at less than room temperature had a devastating effect on the graphite and the material inside. The CTEs (coefficient of thermal expansion) of the different materials (graphite and precious metal) was a possible cause of this failure. Different CTEs can be problematic since the graphite and the precious metal expand and contract at different rates. In this case, though, our graphite grade had the necessary properties to work with the precious metal inside the ingot without failure.
Thermal shock was the true culprit. A material’s thermal shock resistance is its ability to be subjected to sudden thermal gradients without weakening or fracturing. Graphite in general is excellent in resisting thermal shock. Properties such as high strength, low modulus of elasticity, and low coefficient of thermal expansion help graphite prevent thermal shock.
The graphite material we were using was a very good ISO-Molded grade. This material had a small particle size, high density, low porosity, and high compressive and tensile strength. This graphite material worked well for years in their application. However, dense materials with small particle size and low porosity do have higher CTEs. The high density and low porosity of the material means that the particles have less space to expand.
/The inverted cooling process that the customer was applying to the material in this line did not lend itself well to this material. Due to the large volume of the ingot, the rapid cooling had the effect of cooling the graphite first, while the precious metal inside was still at very elevated temperatures. Basically, the graphite was sandwiched between a cold plate and molten metal. Because of the graphite’s high density and low porosity, it cracked to relieve the stress.
The in-house cooling process could not easily be adjusted, so the focus was on finding the right graphite grade for the process. We tailored our choice of graphite to this particular cooling process, selecting one of the few ISO-Moled grades that has an increased porosity. Though this graphite material was designed for a totally different application, where porosity was necessary, it fit our needs in this case perfectly. It allowed for the additional thermal expansion necessary in this process. We also slightly adjusted the cooling process by adding a few minutes delay in the rapid cooling process (which took the upper temperatures down a bit). The final result is a process that is working smoothly.
Proper understanding of material properties, and proper understanding of process, allowed us to tailor our offer to this customer. Our graphite specialists, deeply experienced in solving these types of problems, made all the difference here. Six months down the road, the customer is still happy. No failures, no delays in the production line. This story of dedicated customer service is the epitome of what we do at Semco.