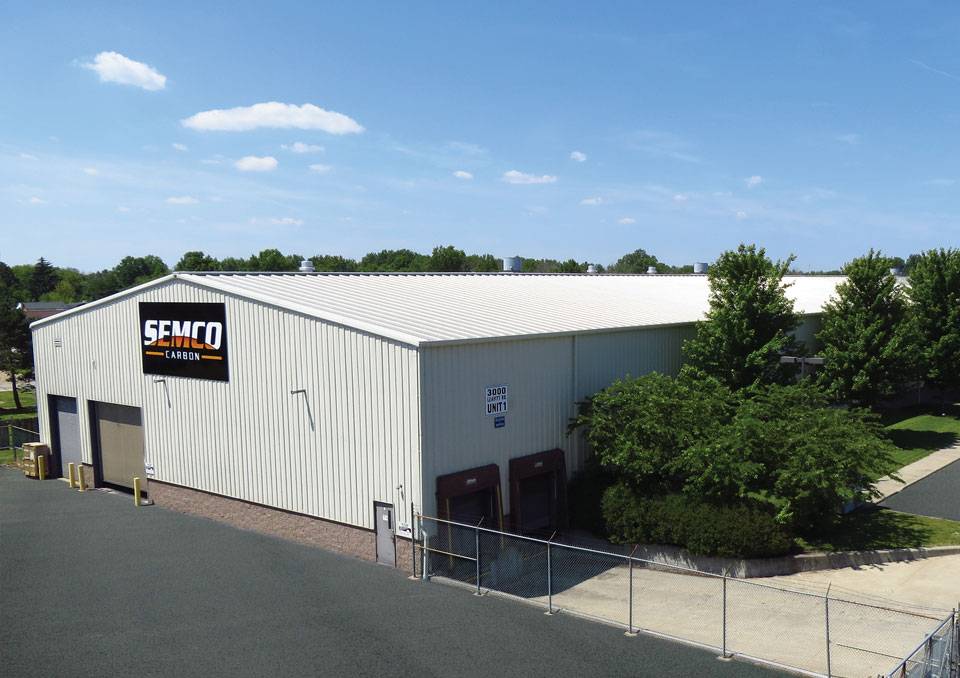
Semco Carbon and Indoor Storage of Graphite
As you’re probably aware, at Semco we really love graphite. It is an incredibly versatile material with so many applications in various industries. We keep a lot of it on hand at our manufacturing facility in Ohio. Partly, as we’ve detailed in several blogs this year, our stocking of various grades of graphite is meant as a hedge against an unpredictable international market. We also like to have material on hand so that we can begin production quickly when a client comes to us with a graphite machining order. Our customers frequently ask us about storage of graphite material, both how we store it and how they can store any material they purchase. Graphite material can technically be stored outside, without structural damage. Unlike most materials, graphite is capable of withstanding long winters or hot days equally well. With that being said, there are some things to think about when deciding where to keep that extra graphite you plan to machine in the future. This blog will detail one particularly important consideration in graphite storage.
The first and most important thing to remember about graphite is that it is porous. Due to its porosity (7%-13%), graphite does absorb water. For this reason, graphite materials should not be left out in the rain or snow. It’s not that water seeping into the graphite will permanently ruin the material -- it won’t. Proper drying cures any issues. Drying out large blocks of graphite, however, is much easier said than done. Depending on the grade and size of the graphite material, the time necessary to properly dry it out can extend into months, especially in the middle of the winter. For the simple reason that drying graphite is incredibly time-consuming, we make sure to keep our stock very dry. Imagine explaining to a customer, after all, that their order can’t be completed just now because their material is drying out. Things get even worse if you attempt to machine graphite that has wet areas within its volume, or material that is completely wet. The byproduct of machining graphite is graphite dust, which we collect into dry bags through a relatively complicated dust collection system. Introduce water or fluids into the mix, and what you have is a mess. Not only is the tooling not able to cut the material properly, but the collection system is also not able to collect because it gets clogged by an impossible-to-clean slurry.
So while graphite can technically be stored outside, then dried, practical reasons dictate that graphite should be stored inside. Prioritizing dry storage has always been our practice at Semco. When we relocated to our newest facility, roughly half the space in the facility was allocated to graphite material storage. Between floor space and shelves, more than 20,000 ft² of space is dedicated to storage. That allows us to store upwards of 300 tons of graphite in a dry, controlled environment. In the 7 years since we moved, Semco has grown significantly. Our 50,000 ft² facility, which we have never imagined would be insufficient, is now full to capacity. Between our graphite machining area and the storage area, no space is left. The next logical step for us is to expand. Although not yet built, we are actively planning additional warehouse space to store material. To best serve our customers, it is Semco’s priority to store and maintain our raw materials in ready-to-machine condition. Our customers deserve the best, and Semco is determined to provide the best.