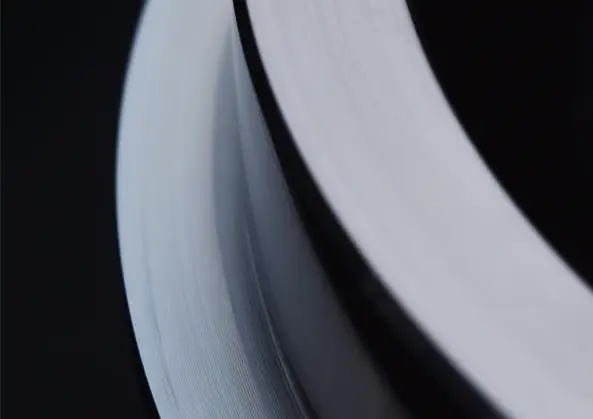
Machining Synthetic Graphite
Machining graphite material, be it synthetic or natural graphite, requires the same type of CNC machines as does, say, machining steel or aluminum. When cutting graphite material, though, there are very important distinctions as to how the machines are actually set-up in order to properly perform. Particularly in the synthetic graphite manufacturing process, there are risks to cutting graphite material in a shop unequipped for machining graphite. At Semco, machining graphite material is precisely what we are equipped for.
Machining synthetic or natural graphite requires specific equipment and tools to achieve precision and to minimize the risk of contamination. Synthetic graphite, for instance, is a brittle and abrasive material. Cutting graphite material can generate fine dust particles, which can be harmful if inhaled. Our shop protects its employees and machines from graphite dust. We also have multiple departments handling specific machining operations. The main ones are the lathe dept., milling dept, and grinding department, all complemented by a large saw department. Whatever the shape, contours, and features of your needed component, our lathe, milling, grinding, and saw departments will get it exactly right.
Departments
Lathes
A lathe is used for turning operations, such as facing, contouring, and drilling. All our lathes are CNC machines that allow for precise control over the dimensions and shapes of the graphite workpiece.
Milling
A milling machine can be used for operations like milling, drilling, and slotting. As with our lathes, our milling machines are CNC machines essential for creating complex shapes and features in synthetic graphite.
Grinding
Grinding machines, such as surface grinders or cylindrical grinders, are used to achieve tight tolerances and a fine surface finish on synthetic graphite components. They are crucial for producing high-precision parts from graphite material.
Saw
Our saw department uses high-speed steel (HSS) or carbide cutting tools for machining synthetic graphite. Our diamond-coated tools are also suitable for cutting and grinding operations due to their abrasion resistance. Proper tool holders and workholding devices, such as chucks and collets, are essential to securely hold the graphite workpiece in place and ensure stable machining.
Dry Machining
One of the most important differences in the manufacturing processes of machining graphite vs. machining metals is the fact that machining graphite is done dry (with no coolant). This kind of machining produces a large amount of graphite dust. Hence, Semco constructed a robust dust collection system to deal with this inevitable by-product of dry graphite machining.
The fine graphite dust that cutting graphite material, or machining it in any way, generates can be hazardous to the health of shop floor employees and to our machining equipment. Our dust collection system with HEPA filters is designed to capture and contain the dust and prevent its dispersion. Our machinists wear appropriate Personal Protective Equipment (PPE), including safety glasses, dust masks, gloves, and protective clothing to prevent exposure to graphite dust and particles.
If you have a machining shop with CNC machines designed to cut metal, and you need a graphite component, remember to send the design for that component to the graphite experts at Semco. If your shop isn’t set up for graphite machining, a lot can go wrong if you try your hand at machining graphite material.