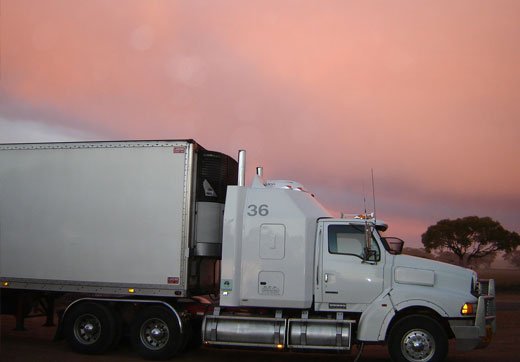
Measuring On-Time Delivery and Scrap Rates
Good businesses will find ways to synergize efficiency and incentives, creating feedback between the two that benefits customers, employees, and the bottom line. At Semco, we have developed a measuring and incentives system to improve our delivery times and to reduce our scrap rates. Semco knows graphite applications, which means we know how important is it that your graphite products be precisely machined according to your specifications the first time. We also know how important speedy delivery is to our customers—when you need a graphite component to keep up production, you need it fast. We started our measuring program to ensure that our scrap rates are low and our delivery times are fast. By minimizing mistakes in the manufacturing process, we can get your component to you faster while saving poorly machined graphite from the scrap heap. Our employees are incentivized to bring their many skills to bear on every project so that any possible hitch in the ordering, manufacturing, and delivery processes are tackled and solved. Ultimately, when Semco saves time and money, so do our customers.
Graphite Products
While Semco’s reputation for excellence in machining graphite products is something we are all proud of, we refuse to rest on our laurels (which is why we’ve maintained this reputation). Reflection and innovation are a constant at our business. In the interrelated areas of scrap rates and delivery times, there really isn’t a ceiling for how good our business could be (while we do concede that we’ll never deliver graphite components instantaneously after an order). To make the incremental improvements that compound and lead to big savings for customers, we began carefully tracking and quantifying scrap rates and delivery times. A scrap rate is the percentage of material or product that must be discarded due to errors in the manufacturing process or flaws in the raw material. While the complexities of the graphite manufacturing process are myriad, suffice it to say that when our employees are fully invested in each project and are offered incentives for lowering the scrap rate for any project they work on, magic happens. Our employees are awarded for their minute attention to every step of the manufacturing process with paid time off and other incentives. It’s not rocket science—if you treat your employees well and attach value to their utmost efforts, both process and product will increase in quality. Our system carefully tracks scrap rates for each project and our employees are given this data as a tool in the search for greater efficiencies.
Graphite Applications
Errors in the manufacturing process can result in delayed delivery times—if a component must be re-machined due to a flaw in the process, our customer is left in the lurch. So many graphite applications are in manufacturing, which means that if a customer is waiting for us to re-machine an important graphite product, their entire production system could be stalled. For each project, therefore, we measure our delivery times to ensure on-time delivery to our customers. Quantifying delivery times means measuring several aspects of our business, not just the machine shop’s work. Once a customer’s order has been machined, it must be packaged, loaded, and shipped. Therefore, we track our warehouse operations, where bottlenecks can occur that are as costly as ones in manufacturing. Our goal at Semco is to make each stage of the process more efficient, saving time and money. With the exception of asking our drivers to speed, there are few things we don’t consider when thinking about how to get our customers’ expertly machined graphite products to them on time.