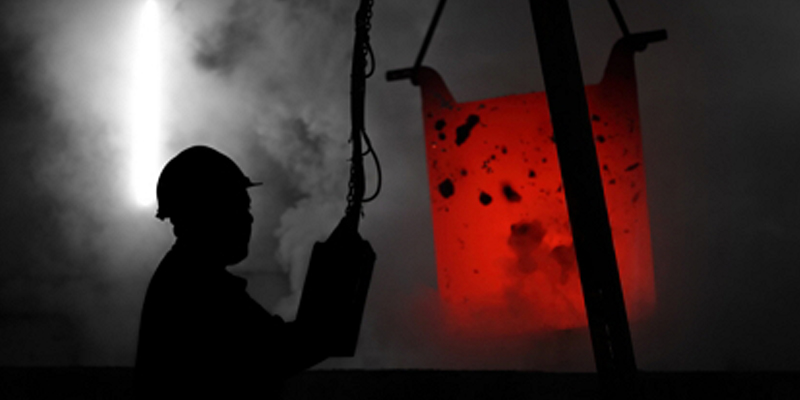
Metal Casting Molds at Semco Carbon
What are Metal Casting Molds?
Metal casting is a 7,000-year-old process used in both manufacturing and fine art. Graphite production is now a key part of this very old process. While casting metals, molten metal is transferred from crucibles into metal molds to create positive metal cast objects. After a metal is poured into a mold, both are then cooled and the metal object is removed and finished.
Move forward a few thousand years and the place of graphite production in metal casting molds becomes more apparent, especially in the process called continuous casting. Continuous casting is a casting method used in high volume production of metals with a constant cross-section. The method uses an open-ended graphite die which is surrounded by a copper jacket. Molten metal is poured through this die. The metal casting mold is typically water cooled, allowing the molten metal to solidify within the die. The custom solid metal form is then extracted from the mold and passed through rollers and water sprays. This process for casting metals removes the heat from the metal and gradually solidifies it.
Graphite is a widely used material in continuous casting. The die molds are generally produced out of graphite. In these types of applications, ISO-Molded graphite types are used to create these graphite molds. Small porosities and good machinability are required properties, and ISO-molded graphite has those. In rare instances, where large ingots are produced, extruded graphite is used in the casting process. The majority of the continuous casting molds are graphite molds produced in 2-piece assemblies, held together by bolts and nuts or by pins.
Graphite Production Case Study
One new customer came to us with a big issue they were experiencing with the molds for casting metals produced by one of our competitors. Once the die was in use, the molten material would slip in between the mating parts, and instead of casting through the opening, some of the molten metal would flow through the sides, damaging the cooling system and making it extremely difficult to collect the lost precious metals. The flaw in the dies also stopped the actual process in its tracks. We received an urgent call and learned that the customer’s production was on hold. Four of these dies were already on their way for us to diagnose and repair, the caller said. That was a surprise. Usually, we evaluate a problem first, then quote a price. Only once that is agreed to do we produce or repair a component. In this case, though, the situation was dire. Coincidentally, we were already in possession of one of their dies, for study. Our engineers had not yet inspected it, so this became our first order of business. Our thinking was that we might be able to figure out what was wrong with the die, fix it, and return it to the customer before we even received the ones they have sent.
Our Quality Control Team went to work, and half hour later the die was disassembled. Another half hour of inspection and we had our verdict: the mating surfaces of the assembly were not flat. Now, by “not flat,” we are talking 0.0015”, which is about the width of half a human hair. Miniscule, but not really when it is precious metals such as gold casting we’re talking about. That 0.0015” is large enough for some of the precious metals to escape the metal casting mold, and no one wants their precious metals escaping anywhere.
After a quick conversation with the customer, we put the graphite production team to work. They ground both mating surfaces within a couple tenths, reassembled the die, and as the driver arrived with the additional 4 dies, this one was ready to go back with him. Their production line was up and running the same evening with no more loss of valuable precious metals. This was on a Friday. Monday morning, we had an e-mail from the customer in our inbox:
“From everyone here we say WOW!! Thank you. Great work by your team.”
The Team at Semco Carbon Comes Through Again!
The die worked flawlessly, and was still casting material. Needless to say, the customer was ecstatic to not be wasting precious metals. We delivered, and they were up and running. There were no P.O.s, no quotes, just Semco coming through for a customer in need. Paperwork was handled afterwards. Problem Solved!