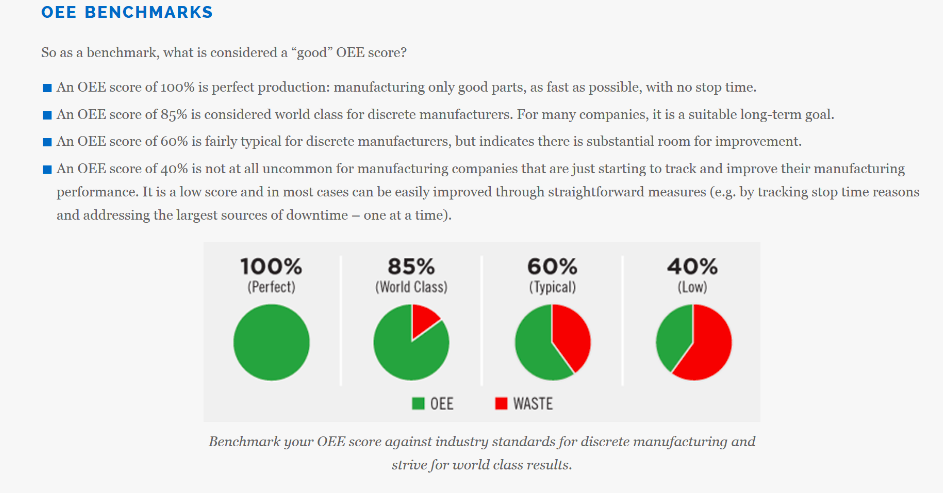
OLE: Overall Labor Effectiveness
Businesses, it is frequently said, run on data. From targeting specific audiences for online advertisements to running sophisticated cost comparisons, contemporary businesses crunch a lot of data to maximize profits. Much of that data comes from within the company itself, as the performance of salesmen, marketing departments, and managers is tracked and subsequent adjustments to strategy or personel is made. In the manufacturing sector, it is common (even necessary) to carefully track the performance of equipment. A program for doing this is called OEE, or Overall Equipment Effectiveness. An OEE program helps provide the management with valuable hard data on their equipment’s efficiency. The chart below gives an idea of the kinds of data that an OEE program can provide to management.
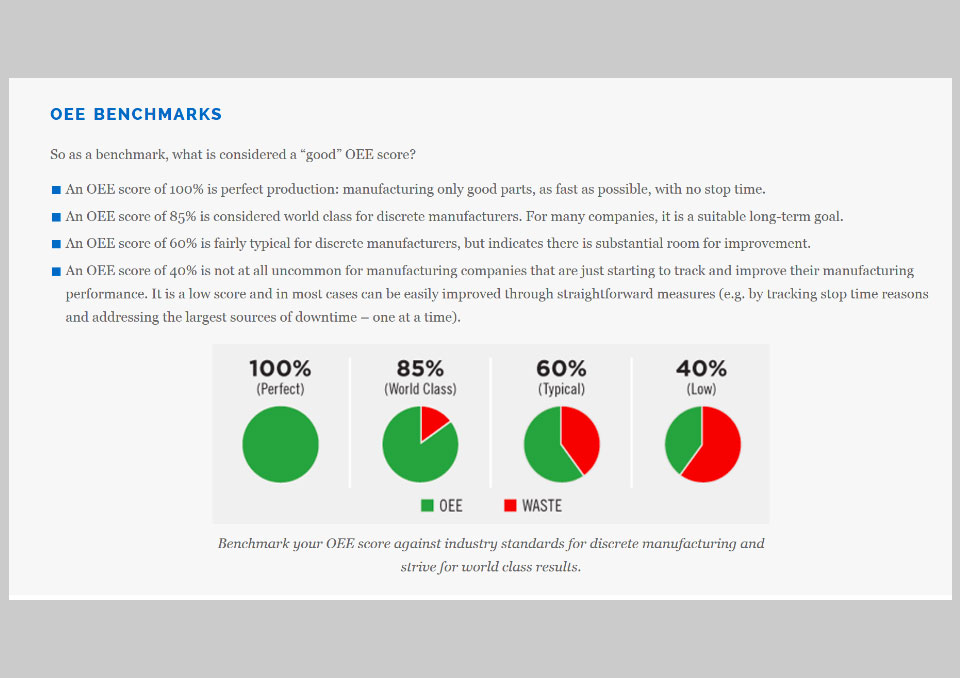
OEEs are great for some manufacturing companies, especially ones with a high degree of repeatability in their manufacturing processes. OEEs are not ideal, though, for a custom graphite manufacturing company like Semco due to our highly specialized products and one offs that we machine for our clients. In the place of an OEE program, Semco has invested in a hybrid program called OLE, or Overall Labor Effectiveness. Rather than track the efficiency of our machines, Semco tracks and gauges our labor force effectiveness, since that is the main driver for overall effectiveness. While the guidelines for OEE and OLE programs are the same, they vary with regards to the metrics. OLE calculation formulas are specifically designed to track labor effectiveness rather than equipment effectiveness. These metrics measure things like attendance, quality/scrap rates, effective time spent on jobs vs. total time spent in the facility, etc.
Semco’s OLE has been two years in the making, and involved setting benchmarks for what we would measure in order to track labor effectiveness. This process involved implementing tracking and measuring procedures to generate the data for the initial benchmarks. Once benchmarks were in place after the first year of the program, Semco was ready to start determining labor effectiveness using our honed metrics. To give some context to our results, it will help to understand the following:
- A business having an OEE of 40% is not uncommon for manufacturing companies that just started tracking their manufacturing performance.
- A 60% score is the general score for discrete manufacturers, but indicates substantial room for improvement.
- An 85% score is considered world class. It indicates nearly perfect production. This is a suitable goal for companies, long term.
Based on industry standards, we estimated our initial OLE percentage would be above the 40% mark, maybe even above the 60% mark. Turns out that our initial OLE percentage was 80%! Much of the credit for this outstanding number goes to all our other initiatives, such as investment in new equipment and constant training of our workforce. Of course, the quality of our workforce, along with the effectiveness of our CAD and Quality departments, also deserves a lot of credit. We always regard ourselves as a world class custom graphite manufacturing facility. To see our initial percentages being so close to perfect only energized us more.
What we learned from our OLE program is that we did not need to revamp our standard procedures, much less make radical changes. Our culture of professionalism and constant improvement over the past 40 years, coupled with all the initiatives we have put into place in the last decade, put us in a great position. And we are thankful to be where we are as a company. The sluggish economy that we are now experiencing gives the edge to companies that can make quality product as fast as possible, at a competitive price. That is precisely what Semco has been doing.
While Semco is proud of our graphite manufacturing operation, we realized that even our OLE number left room for improvement. From the beginning of the year we have focused on refining rather than revamping our manufacturing processes. And to ensure that our metrics continue to give an accurate assessment of our company’s labor effectiveness, we train our personnel on the importance of accurate reporting, from time spent on a job to the amount of material scrapped during a run. Of course, we also continue to invest in more efficient equipment, allowing our workforce to perform even better.
We see what our workforce has given to this company, and in turn we are rewarding our workforce with additional PTO based on month-to-month performance by individuals and groups. Just in July we awarded 66 hours of additional PTO based on the team performance.
Semco is firmly in the category of world class custom graphite manufacturing facilities. A lot of great work has been done so far, and we will push forward in the same manner that got us here. Our OLE scores are a testament to our commitment to produce great product efficiently. The metric we are most proud of, though, is that our customers are happy with our work.