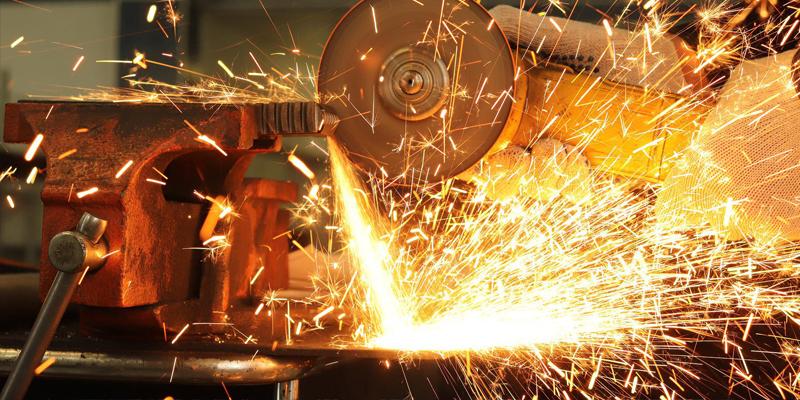
Safety Around Graphite Blocks
At Semco, most if not all processes start with graphite blocks: (sometimes) large sections of (usually) synthetic graphite of various grades. To cut, grind, and shave this material into the components that our customers depend on, our shop floor employees have to pass the material through precise machining processes that bring to bear much friction, pressure, and speed on the material. With all this power and force necessary for machining graphite blocks, Semco has to think carefully about the safety of its shop floor employees. We have a great safety track record at Semco, and in this blog we will explain why that is the case.
Sawing Synthetic Graphite Blocks Safely
The synthetic graphite blocks’ first stop beyond the storage warehouse is almost always the saw department. Here, large blocks or rounds of synthetic graphite are trimmed and partitioned based on each job’s specifications. Since virtually all material used in the facility passes through one of our saws, we naturally make safety in our saw department a priority. By implementing various safety features, we enable our operators to cut material safely. Most of these safety features are built into the actual saws:
Dust Port: This feature channels dust away from the cutting platform and is connected to our dust collector. Dust ports enable dust free operations, better visibility, and good air quality.
Blade Adjustment Knob: This knob helps adjust the cutting blade’s height and position. Allowing the machinist to set the blade at the proper height accommodates the safe handling of specific blocks, which come in many sizes.
Blade: We choose from various blade types, from diamond to carbide. Each choice of blade compound is determined for the specific material grade to be cut, and ensures that the material is cut cleanly and efficiently.
Wheel Guard: This component guards the saw’s wheel inside the frame since the wheel is sharp and can easily cause accidents if left exposed.
Blade Guard: This component guards the spinning blade to prevent an accident or kickback during the job.
Blade Tensioner: The usefulness of this component is in safely ensuring that the blade isn’t too tight when working with softer material. If the blade is too tight, it can cause breakage or possibly slip off the wheels.
Passing Graphite Blocks Safely Through Lathe and Mill
From the saw department, the synthetic graphite material is generally transferred to either the lathe or mill department. Here as well, our machines have various safety features built into them.
For lathes, safety features for machining graphite blocks include the following:
Foot Brake: All lathes have a foot-enabled brake at the bottom of the machine that cuts off the spindle motor mechanically and electronically.
E-Stop Button: The Emergency Stop Button stops the motor electronically, allowing the motor to coast to a stop. This is used in situations where the foot brake is not needed to stop the lathe instantly.
Chuck Guard: All our engine lathes feature a chuck guard that extends around the spindle nose. The chuck guard needs to be in the closed position to start the machine. If you’re running the machine and you lift the chuck guard, it functions like an E-Stop Button and shuts down the spindle.
Doors: All our enclosed lathes have doors present that have to be closed in order to begin the operation.
Many of the same features can be found on the milling machines. E-Stop Buttons are present on all machines, as are guards, doors etc.
Safety Training for Machining Graphite Blocks
In addition to the safety features on the machines, safety procedures are also put in place to keep machinists safe. All operators receive thorough shop safety training. The following is a list of imperatives that are covered in the safety training for saw, lathe, and mill operators.
- Keep all guards in place while operating the machine.
- While operating a machine, allow no one else to touch it.
- Keep hands away from moving cutting tools.
- Only use cutters that are sharp and in good condition.
- Always use the proper cutting fluid for the material being cut.
Before Starting the Mill/Lathe:
- Cutting tools must be securely fastened in the machine spindle with the proper accessory.
- Never try to tighten cutting bits or tools by hand.
- Work pieces and stock must be rigidly fastened to the mill bed with clamps, a vise, or special fixtures.
- Make sure the cutting tool is clear of the material before starting the machine.
- Make sure the cutter is rotating in the proper direction before cutting material.
While in Operation:
- Use appropriate speeds and feeds for the type and size of cutter being used and the material being machined.
- Do not make measurements of the stock while the milling machine is powered.
- Always stay at the machine while it is running.
- Use the milling machine spindle brake to stop the spindle after the power has been turned off.
Maintenance and Housekeeping Imperatives:
- Do not allow large quantities of chips to accumulate around the work piece or machine table.
- After stopping the machine, use a brush or rag to remove all excess chips from the mill bed and stock.
- Do not place anything on the milling machine table such as wrenches, hammers, or tools.
Semco can continue our work of turning large synthetic graphite blocks into precise components for our customers because we take safety so seriously. By ensuring that all machines are equipped with necessary safety features and that all machine shop employees receive thorough training, we make Semco a safe and rewarding place to work.