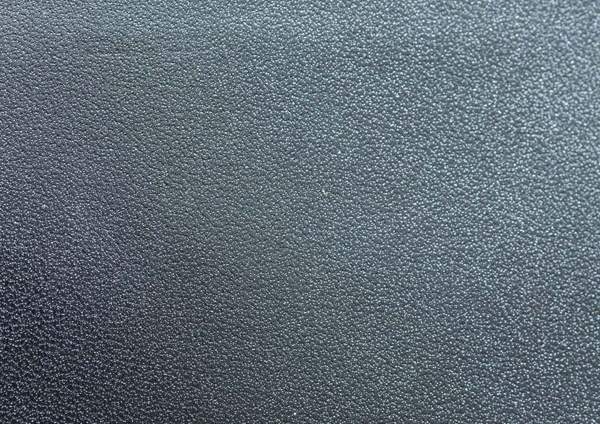
The Challenges of Measuring Surface Finishes
Any surface, from a school desk to a basketball court, has a topography with peaks and valleys. On the surface of the earth, topography is readily apparent (except, maybe, in parts of Kansas). But even the smoothest metal surfaces deviate from a theoretically ideal plane. Recent standardization has resulted in the creation of a standard range (Ra) for surface deviation, measured in micrometers or micro inches. With graphite material, these deviations from a perfect plane are typically more pronounced due to the porous nature of graphite. Those small naturally occurring pores in the material have the effect of increasing the deviation from the ideal plane in surface finish measurements. We do on occasion see prints and documents produced by engineers that work mostly in metal that contain unattainable surface finish callouts, due to the porous quality of graphite. Semco has developed several ways to address this issue to achieve the appropriate surface finish for graphite applications.
Assigning, producing, and measuring surface finish is a function that is mostly associated with closed porosity materials. Materials like steel and aluminum do have pits and valleys, or waviness from the theoretical perfect flat surface, but in a closed porosity environment. In this scenario, all machining operations will be applied with the goal of reducing the waviness, or the high spots. Machining operations for metal have quite well established surfaces finishes. Here are a few examples:
- Sawing - Between 1000 and 32 micro inch
- Planing - Between 500 and 32 micro inch
- Turning - Between 250 and 16 micro inch
- Milling - Between 250 and 8 micro inch
- Grinding - Between 63 and 4 micro inch
- Electro-polishing - Between between 32 and 2 maybe even better
Like any other material, graphite is machined to achieve a surface finish acceptable for particular applications. Some of these surface finishes are difficult, if impossible, to achieve with graphite, particularly with lower graphite grades. The porosity of graphite means that as the material is machined, the delta between peaks and valleys is indeed reduced, but at the same time, more porosity is revealed. In effect, graphite will always have valleys due to its open porosity. One solution to this issue to impregnate graphite with another material such as molten metal, wax, oil, etc. In the impregnation process, the graphite is submerged in the other material, a process that can essentially transform the graphite material into a closed porosity material. If a graphite application requires a flatter surface finish, impregnation is one way to achieve this outcome.
Another approach that Semco takes with our clients is to choose graphite grades that are appropriate for various applications. Graphite grades have varying levels of porosity, with the higher grade material more dense and thus less porous. If we are working on a graphite application with a client that requires just a small reduction in porosity, choosing one of the many graphite grades that are available might do the trick. Since Semco stocks many grades of graphite at its warehouse, clients are frequently spared the wait of ordering a different graphite grade from a distant manufacturer.
If your company’s graphite application requires smooth surface finishes, we flat have you covered at Semco.