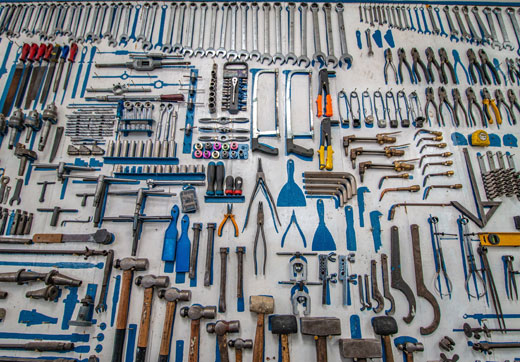
The Importance of Maintenance in Graphite Machining
At Semco, carbon graphite is king. That material that makes up all our graphite components is the star of our graphite fabrication story. A less discussed, but critically important, subject in our story of graphite fabrication is graphite machining maintenance. The high quality of the graphite components we manufacture depends on the proper functioning of our machines. Semco is dedicated to keeping these machines running efficiently and producing quality graphite parts from carbon graphite. Hence, we have implemented scheduled maintenance for all our equipment done on site by our knowledgeable employees. Occasionally, when our state-of-the-art, complex machines have breakdowns that go beyond the expertise of our shop floor employees, we rely on companies with highly specialized knowledge. In general, though, Semco is able to handle bumps in the road of graphite fabrication, or, more accurately, we keep these bumps from ever happening through our process of industrial maintenance.
Industrial maintenance, also called plant maintenance, is the process of implementing processes to reduce breakdowns, increase uptime, and promote overall reliability. In other words, maintenance is the general process of ensuring that assets are kept in good working condition. When a piece of equipment keeps running at its expected capacity, production operations are sustained. Having a maintenance plan reduces maintenance costs, maximizes uptime potential, and ultimately increases profitability. Our maintenance plan can identify maintenance tasks that prevent failures in the first place, saving our company more in the long term.
In this blog, we offer a brief explanation of two types of maintenance we do in the shop, as well as the benefits to our graphite fabrication process of thinking through our maintenance practice.
Preventive Maintenance in Graphite Machining
The goal of having a more proactive approach in maintenance is to mitigate potential causes of failure before they even occur. A preventive maintenance (PM) strategy requires doing tasks proactively according to a usage- or calendar-based schedule. PM tasks can significantly reduce unplanned downtime by avoiding conditions that cause breakdowns. Our graphite components are more likely to be machined on time and to the customers’ specifications when our machines are kept up regularly. PM also reduces the risk of catastrophic failure that might occur should a reactive approach be adopted in our graphite fabrication operation. By investing in a PM strategy, maintenance costs are reduced compared to a hypothetical situation where we simply react to machine breakdowns.
Reactive Maintenance in Graphite Machining
Although we try to avoid reactive maintenance as much as possible, there are instances when we have to use it.
As the name suggests, reactive maintenance is concerned with tasks that occur after a piece of equipment breaks down. The advantage of reactive maintenance is that the initial costs are significantly lower. Maintenance tasks are only carried out when a machine is already showing signs of poor performance in machining graphite components.
The downsides of reactive maintenance generally outweigh the short-term benefits. The cost of performing no or minimal maintenance is the likelihood of irreversible damage from sudden failure. Since machining carbon graphite requires machines that exert a great amount of force in sometimes high-heat or otherwise extreme environments, wear and tear on machines is inevitable. If they are not cared for, our machines will eventually fail. These failures typically result in production losses, with worse cases leading to the damage of critical equipment. These machines are essential assets to our operations, so we perform reactive maintenance only as a last resort.