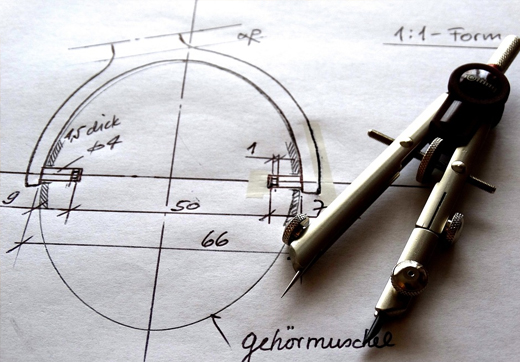
The Tech Side of Graphite Fabrication
Your business is designing a manufacturing set-up. One of the constituent parts will be exposed to various chemicals and high heat. Graphite is considered for this part because it is chemically inert and stands up to extreme temperatures without degrading. Engineers make a mock-up of this manufacturing set-up and they Zoom call us at Semco.
Customer: “Hi, we finished the mock-up of the apparatus and it looks like we’ll need a graphite mold about 7 or 8 inches long that looks kinda like this (holds up napkin drawing of future graphite component).
Semco engineer: “That’s a nice drawing. Could you text a picture of that to us so we can examine it more closely. Also, tell us more about how it will fit into the larger set-up.”
Customer: Well, it will attach here (points to scale model on the table) and will receive the molten metal poured from here (points to different part of the scale model).
The question that non-manufacturing types might have at this point is, how do graphite components like this one go from a vague idea in an engineer’s head to a slightly less vague mock-up to a precisely machined component? Well, these are the secrets of graphite fabrication. Don’t worry -- since you’re reading this blog, we won’t keep it a secret from you.
The simple answer to how Semco and the client determine the dimensions and appropriate material grade for graphite components is, teamwork. Semco engineers and the clients form a team that talk through possibilities and scenarios until we know enough about what is needed to design the piece. Then our own team at Semco takes over. Our CAD/CAM techs digitally model our customer’s parts and assemblies with a powerful modeling and prototyping program called Solidworks. (In case you’re not an acronym person, those last two stand for Computer-Aided Design and Computer-Aided Manufacturing, respectively). We also use Solidworks to create approval, production, and spec drawings as needed for each particular application. Mastercam is used to create the programs to safely and efficiently machine the parts.
This last bit of teamwork is the crucial one: the collaboration of human and machine. These kinds of teams require great precision on the part of the machine and a lot of hands-on training by the human. Each CNC Machinist has experience on a multitude of machines (ahem, pardon our acronyms. CNC means Computerized Numerical Control, which really tells you nothing. Basically, CNC is a fancy process that uses computers to manufacture things). Because of the advanced technical knowledge needed to operate CNC technology, our CNC machinists go through hours of training on their machine’s Operation and Command systems before being allowed to run them. And, of course, they spend a lot of time on safety training. These are friendly machines, but not if you get in their way when they’re working.
There is another way we can help customers get the graphite component they need. When a customer needs an identical part to one they already have, they can just send us the part. Even if the part is damaged and the customer needs it replaced, we will take that too. The talented graphite specialists in the our Quality Assurance Department have the capability to reverse engineer these parts. We then create a digital solid and drawings from the recovered data so that it is easy for the customer to order this part the next time it is needed.
At Semco, we are constantly striving to keep up-to-date on the latest technologies. But if all you’ve got is a drawing of a great idea on a bar napkin, we can start there too.