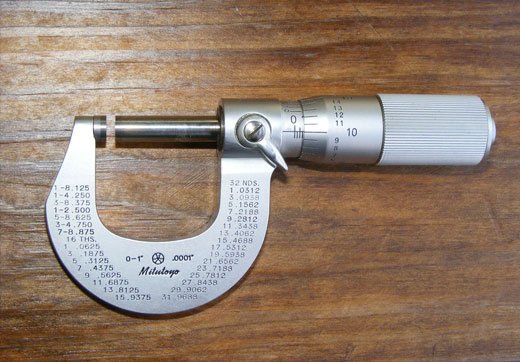
Tolerance Stackup
As our readers can see from this blog, we love to talk about what we do at Semco, which means a lot about graphite manufacturing. We enjoy sharing with our clients and others in the industry how we run our graphite machining operation on our shop floor, what our employees thrive at outside of work, where we source our graphite material from, and how we perfect the graphite products we machine for our clients. We have shared our opinion on tariffs and examined reasons why we prefer to provide our clients with the raw material for manufacturing. As engineers, what we really love to talk about it technical stuff. So fair warning, this blog will examine issues our clients have faced with tolerancing stackup in their assemblies. We don’t claim that tolerancing stackup is the most exciting topic (unless you’re an engineer!), but understanding how variation in component dimensions can affect an assembly is critical for that assembly to perform properly. Now to the technical stuff and a case study.
Tolerancing is a system for describing the acceptable variation in physical dimensions of a manufactured material or component. Essentially, tolerancing begins with the acknowledgement that variables, such as environment, material quality, and machining processes, can and will affect the dimensions of whatever component is being manufactured. This variation needs to be taken into account by engineers so that an assembly can be built that can absorb these variations and still work properly. It is important to remember that tolerance is not a design specification of a component--rather, it is a tool of quality control used to ensure that components fall within a certain dimensional range around the desired design specs. Further, engineers must keep in mind that tolerances accumulate in an assembly. In complex 2D and 3D assemblies, computer models are usually needed to calculate cumulative tolerances. In a linear assembly, however, engineers can normally determine the accumulation of tolerances of the individual components, or what we call “tolerance stackup.”
Recently, one of our clients encountered a problem assembling graphite products that we manufactured. Solving this issue with our client meant thinking about tolerancing and, in particular, tolerance stackup. We completed a large order of graphite discs for this client. The components were relatively simple: a disc, with a couple step-downs on each face of the disc. The dimensions were specified for each step, with tolerances applied to each step. In essence, the O.A.L. (overall length) of the part was represented on the print as a collection of dimensions, linearly added, without the actual O.A.L. being dimensioned on the print. The print had a general tolerance of (+/-0.005’’), which means that the tolerance applied to all dimensions on the print.
During production of these components, we applied rigorous quality control at each step of the graphite manufacturing process. We machined a first article, measured in tolerance, did inprocess inspections throughout the run, measured in tolerance, did a final inspection, measured in tolerance. We shipped the parts to the customer, and to our surprise, a couple months later, the customer called to say that some of the parts were out tolerance. They specifically referenced the O.A.L. as being out of tolerance. The first thing we did was to investigate this complaint was to review the print provided by the client, where we observed that the O.A.L. was a calculated dimension, and was not listed on the print as a discrete dimension. The customer’s expectation was that the O.A.L. would be within the (+/-0.005’’) marked on the print as general tolerance. Unfortunately, the customer’s assumption in this instance was incorrect, as was the print. What the customer did not take into account was that the O.A.L. is a critical dimension. Instead, they dimensioned all the steps that added to the O.A.L.
Semco takes problems that our clients bring to us very seriously. In this instance, we took a trip to the customer’s facility and inspected the parts, per print. Our customer’s quantity department personnel were present at this inspection. Every single dimension present on the print was measured, and measured in tolerance. What was observed during this inspection was that most of the dimensions measured were in the upper range of the tolerance, hence when all were added, the result was an O.A.L. way over the (+0.005) upper limit the customer expected. This is a clear example of an issue created by tolerance stackup, where these minute variations were not properly accounted for and ended up affecting the functioning of an assembly. We worked with the customer on a solution that included machining a few thousandths (NEED A UNIT OF MEASUREMENT HERE) off of each face of the part, in effect reducing the O.A.L. to an acceptable level. We also worked with the customer to revise the print. The revised print included the O.A.L. distinctly called out on the print (hence, the +/-0.005’’ tolerance was applied). Subsequently, we machined parts per the revised print. We are very happy to report that no more issues were signaled after we applied this solution to the issue.
There are some important takeaways from this story. First of all, tolerance stackup is a normal consequence of how dimensions are called out on the print. There’s really no avoiding it. Therefore, it must be properly accounted for during graphite machining, or it can have unintended consequences. If the prints are not dimensioned correctly, or if critical dimensions are omitted from the print (just because they can be calculated), then total variation of dimension, which is of course based on individual variation of components, can get out of hand.
Another day at Semco, another graphite manufacturing problem solved. Man, we love this stuff.