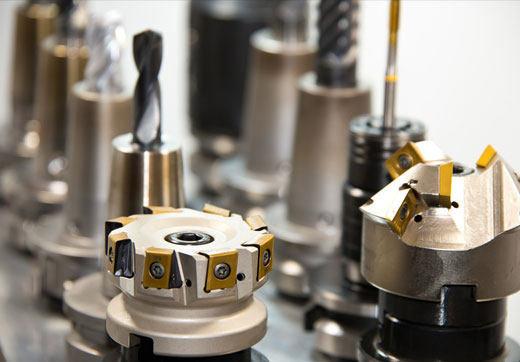
Tooling Project
Graphite Manufacturing
Graphite manufacturing is a complex business, especially for a company that specializes in custom orders. At Semco, a focus of our graphite production business is tooling graphite components to fit our clients’ specialized needs. To keep our production thrumming and our clients informed, we have plenty of raw material on hand and a system that tracks every step of the manufacturing process to keep the client up-to-speed on the progress of their order.
As satisfied as our clients are, we don’t believe in resting on our laurels as an industry leader in graphite manufacturing. We analyzed ourproduction process to search for any slack in the system, and identified graphite tools—end mills, face mills, reamers, drills, etc—and, more specifically, our practice of ordering these tools, as an aspect of our supply chain that could be tightened up. Our tooling project, which we devised to address the issue of inventory and ordering of tools used in graphite production, has translated to savings in the tens of thousands of dollars, savings that Semco passes on to its customers.
Graphite Production
With our cumulative decades of experience in graphite manufacturing, we have stockpiled a great deal of knowledge that we leverage to create the most efficient and highest quality experience for our clients. Our employees, many of whom have been with the company for years or even decades, have accumulated experiential knowledge of the graphite manufacturing process that, when tapped, yields greater efficiencies in the process and higher quality in the product. Some of that untapped knowledge residing with our employees was the knowledge of the lifespan of tools for machining graphite and how often these tools require replacing. Our employees were skilled at recognizing when a new tool would be needed. However, we lacked a comprehensive tracking system for replacement tools. This resulted in orders, and re-orders, of parts which we already had in stock. What we required, our analysis showed, was a tracking system that would maximize our knowledge of graphite tooling inventory, which in turn would leverage our employees’ experiential knowledge of when new tools or parts would be needed. Now, if our graphite experts recognized the need for a new face mill to plane broad graphite surfaces, rather than immediately order a new saw, we could search our entire manufacturing facility for the needed saw. In some cases, we have the tools on site and thus save the unnecessary expense and time of a redundant order.
Graphite Tools
Initiating this tooling project meant identifying, quantifying, and labeling all tools. Each tool was assigned a number and entered into our system. Whenever a new tool is required by our manufacturing division, the need is run through this system. If we don’t have the tool on site, we order a new one. If we do have the tool on site, it is immediately identified and integrated into the graphite production process. We replicated this system for AI tools as well, so that all AI tools are catalogued and linked to our quoting/order entry system. The benefits of this system for the client are not only in cost, but in time as well. Replacing a tool with an identical one on site saves a great deal of time. The production process need not delay if the replacement tool is in our facility. With fewer orders for replacement tools to process, our ordering is more streamlined and efficient. With our tool inventory catalogued, we can automatically assign tools to a project from the quoting stage. Once a project becomes active, the tools needed would be ordered and ready for when the project hits production.
Our tooling project is one of the many positive outcomes produced by rigorous analysis of our own business and manufacturing practices. Ultimately, the care we take in thinking through all aspects of our business pays off for our clients in the form of faster production of higher quality components at lower costs.