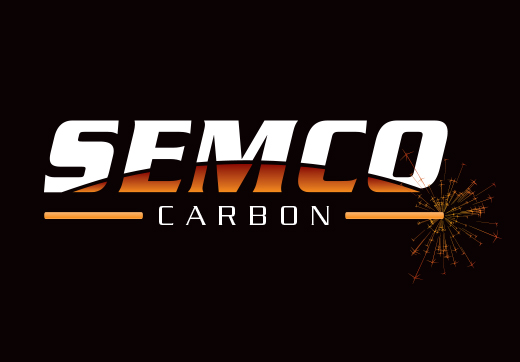
Vacuum Furnace
We have created this post for you, the maintenance supervisor that just had one relatively inexpensive part break, causing your vacuum furnace to be down for an extended amount of time. All because the component was not in stock. We have created it for the owner or the engineer in charge of production who does not want to find himself in the afore mentioned situation.
What is a vacuum furnace? A vacuum furnace is a type of furnace that can heat materials to very high temperatures. The function is to carry out processes such as heat treatment, sintering or brazing. The area where the heat is produced is called a hot zone. Since the early development of the vacuum furnace, engineers and thermal experts have tried to improve the insulating characteristics and the performance of the components inside the hot zone. Most of the early designs of vacuum furnaces used an all-metal design. As vacuum furnaces became an important production tool, alternate materials have been used with various success.
The most acceptable types of hot zones manufactured today use graphite in the form of sheets, felt or board for insulating purposes as well as graphite components such as heating elements, connectors and furnace bases. The multitude of acceptable graphite grades available along with graphitic insulating components, offer the end user a wide selection of advanced materials options.
Utilizing the appropriate materials to place in service is of key importance and will change with each particular application. Choosing the correct materials will result in controlled atmosphere and vacuum furnaces capable of running at uniform temperatures up to 5250°F+ with low contamination and minimizing power losses.
As graphite emerged as a highly engineered advance material, the use of this material in manufacturing hot zone components increased. Along with advanced material design the vacuum furnace manufactures made efforts to reduce the size shape and weight of the hot zone components to increase efficiency. Graphite hot zone components allow for intricate part designs that can be manufactured fast and reliably.
I would like to discuss the challenges that arise in the production of graphite components by using the arc element as an example. Simple, right? The arc elements purpose is to get hot, reliably and consistently from element to element, end of story. Well, if we are discussing arc elements, we need to introduce another factor, electrical resistance. We already know that we are working with multiple graphite grades. Normally, we have requirements regarding basic dimensions and a target resistance. A lot of our customers believe that a print is sufficient in producing these components. Not quite so. Going back to the electrical resistance , the challenge is to take a potential variable and transform it into a constant. That is the only way the vacuum furnace will produce constant temperatures and run efficiently. While having multiple graphite grades is great, it is also a challenge. Every grade has different electrical resistance. It is important to note that a arc elements basic dimensions do affect its final electrical resistance.
Thinner components have an increased resistivity versus thicker ones. And then there is the location where the resistance is measured. Measure in one location and the values are totally different than if the measurement is taken in a different location. So, it really is not so simple, the sum of all these variables can pose a challenge for the uninitiated. Graphite vendors need to have a good understanding of all these factors, choosing the right materials, understanding basic dimensions and how does resistance change as the dimensions change.
It is important for both the customer an vendor to clearly define how and where is the target resistance measured. Defining these parameters is critical in producing a element that will that will work correctly. The challenge is on the vendor to provide a not only a quality product, but to help educate the customer so that a informed decision is possible and appropriate parameters are established.
Attached below is a video showing resistance testing of a graphite arc element at various location and the corresponding change in measured electrical resistivity.